FROM the frequent mention of
linen in the history of Scotland, it is evident that the inhabitants were
acquainted with the processes of making cloth from flax six hundred years
ago at least. It is related that, at the battle of Bannockburn (fought in
the year 1314), "the carters, wainmen, lackeys, and women put on shirts,
smocks, and other white linens, aloft upon their usual garments, and bound
towels and napkins on their spears, staves, &c. Then placing themselves in
battle array, and making a great show, they came down the hillside in face
of the enemy with much noise and clamour. The English, supposing them to be
a reinforcement coming to the Scots, turned and fled." There is good reason
for concluding that the linen so successfully displayed on this memorable
occasion was home-made. At first the flax was grown, dressed, spun, and
woven by the people for their own use; but towards the close of the
sixteenth century linen goods formed the chief part of the exports from
Scotland to foreign countries. About the same time a considerable quantity
of Scotch linen found its way into England. Several attempts were made to
establish linen manufactories, so that the trade might be extended and
carried on more profitably; but the promoters, though encouraged by royal
favours and the concession of certain privileges, did not succeed. Efforts
were made to improve and extend the woollen manufactures of Scotland by
various legislative enactments, one of which prohibited the importation of
woollen – — cloths from England. The English people retaliated for this
interference with their trade by treating the men who sold Scotch linen in
their territory as malefactors, whipping them, and making them give bonds
that they would discontinue the traffic. This told seriously on the working
population of Scotland, for it was calculated that from 10,000 to 12,000
persons were employed in making linen goods for the English market. An
appeal to the king had the effect of removing the restrictions on the trade.
In 1686 the first Parliament of James VII. passed an "Act for Burying in
Scots Linen," the object of which was to encourage the linen manufacturers
in the kingdom, and prevent the exportation of the monies thereof by
importing linen. It was enacted that "hereafter no corpse of any persons
whatsoever shall be buried in any shirt, sheet, or anything else except in
plain linen, or cloth of hards, made and spun within the kingdom, without
lace or point." Heavy penalties were attached to breaches of the Act, and it
was made the duty of the parish minister to receive and record certificates
of the fact that all bodies were buried as directed.
It would appear that the
weavers, in order to increase their gains, had, towards the end of the
seventeenth century, begun to make linen cloth of inferior quality, and
Parliament interposed to put a stop to that practice. In 1693 an Act was
passed "anent the right making and measuring of linen cloth." It set forth
that "the King and Queen's Majesties considering how much the execution of
the good laws for the right making of linen cloth hath been hitherto
neglected, to the prejudice of the lieges, and the loss of trade within this
kingdom, do therefore, with advice and consent of the Estates of Parliament,
ratifie, approve, and confirm all Acts of Parliament made for the right
making and improving of linen cloth." The Act then proceeds to describe
minutely how yarn is to be made up and sold, and how the cloth is to be
woven and measured; and this in consideration of "how much the uniform
working and measuring of linen cloth may raise the value thereof with
natives and strangers, and render the trade more easy and acceptable to
merchants." In order to afford protection against dishonest work, the Act
required " that the owner of all linen cloth made for export, before it be
exposed to the first sale, shall be obliged to bring the same to a royal
burgh where linen is in use to be sold, there to receive the public seal and
stamp of the burgh, bearing the coat-of-arms of the burgh upon both the ends
of ilk piece or half piece thereof, which shall be a sufficient proof of the
just length and breadth, evenness of working, and the due and sufficient
thickness and closeness thereof; and for that effect there shall be in each
royal burgh where linen is in use to be sold, an honest man well seen in the
trade of linen cloth appointed to keep the said seal for marking linen
therewith." The fees to be charged by the stampmaster were also fixed by the
Act, and he was subject to penalties if he neglected his duty. For the
encouragement of all persons who should establish manufactories of linen
cloth it was further "statute and ordained, that all lint, flax, and linen
yarn imported for the use of companies or manufactories, and all linen cloth
exported by them, shall be free of custom duties or excise."
The linen manufacturers of
Scotland derived great advantage from the union with England. The duties
charged on goods exported to the sister kingdom were removed, and at the
same time the colonies were opened to Scottish enterprise. A period of great
industrial activity set in, and the quantity of linen goods produced was
much increased. In 1710 upwards of 1,500,000 yards of linen cloth were
produced. Ten years afterwards England alone took L.200,000 worth of Scotch
linen annually. A great stimulus was given to the trade by the establishment
of the Board of Manufactures in 1727. The fifteenth section of the Treaty of
Union with England, signed in July 1706, stipulated that "L.2000 per annum
for the space of seven years shall be applied towards encouraging and
promoting the manufacture of coarse wool within those shires which produce
the wool," and that " afterwards the same shall be wholly applied towards
the encouraging and promoting of the fisheries and such other manufactures
and improvements in Scotland as may most conduce to the general good of the
United Kingdom; and it is agreed that Her Majesty (Queen Anne) be empowered
to appoint committees who shall be accountable to the Parliament of Great
Britain for disposing the said sum." No action was taken to fulfil the
conditions of this clause of the Treaty until 1727, when an Act was passed
for the appointment of twenty-one commissioners to take charge of the
revenues and annuities allotted to the encouragement of manufactures and
fisheries. By that time the money which was to be devoted to the improvement
of the woollen manufactures had accumulated to the sum of L.14,000; while
L.6000 in addition was due for the other purposes referred to in the section
of the Treaty under notice. The interest on those sums, added to an annuity
of L.2000, placed a considerable amount at the disposal of the "Board of
Trustees for Manufactures," as the commissioners were designated, who laid
before the King in council a triennial plan for the apportionment of the
revenues.—The first plan prepared was for the three years from Christmas
1727, and provided for the expenditure of L.6000 yearly in the following
proportions :—For the herring fisheries, L.2650; for the linen trade,
L.2650; and for spinning and manufacturing coarse tarred wool, L.700. The
money allotted to the linen trade was divided as follows :—Premiums for
growing lint and heffip seed at 15s. per acre, L.1500; encouraging spinning
schools for teaching children to spin lint and hemp, L.150; prizes for
housewives who shall make the best piece of linen cloth, L.200; salaries to
the general riding officers at L.125 each, L.250; salaries to forty lappers
and stampmasters at L.10 each, L.400; expenses of prosecutions, L.100;
procuring models of the best looms and other instruments, L.50. It would
appear from this that technical education is not such a new thing in this
country as some persons suppose—the spinning schools referred to being
places in which a technical knowledge of a certain branch of industry was
imparted to young persons. The sum of L.10 a-year was allotted to the
endowment of each seminary, of which sum the teacher or mistress received
L.5 as salary; L.4, 1s. 8d. was devoted to the purchase of fourteen spinning
wheels, at 5s. 10d. each; 5s. to maintaining pirns, bands, &c.; and the
balance, 13s. 4d., went to provide coal and candles for the session, which
lasted from the 13th October to the 15th April. The spinning schools were
situated chiefly in the Highlands, as the trustees considered it highly
desirable to create habits of industry in those regions where indolence and
poverty reigned supreme.
The Board lost no time in
taking steps for improving the quality of the linen made in Scotland; and
their records show, that one of their first acts was to propose to Nicholas
d'Assaville, cambric weaver, of St Quentin, France, to bring over ten
experienced weavers of cambric, with their families, to settle in this
country, and teach their art to others. The offer was accepted, and the
Board purchased from the Governors of Heriot's Hospital five acres of ground
in Broughton Loan, a suburb of Edinburgh, on which they built houses for the
French weavers. The colony was named Little Picardy, and its site is now
occupied by Picardy Place, which, with York Place, forms the eastward
continuation of Queen Street. The Frenchmen were Protestants, and they began
operations in 1729—the men to teach weaving, and their wives and daughters
the spinning of cambric yarn. A man skilled in all the branches of the linen
trade was at the same time brought from Ireland, and appointed to travel
through the country and instruct the weavers, and others, in the best modes
of making cloth.
It may be interesting to note
a few facts contained in the minutes and annual reports of the Board. In
1728 premiums were offered to persons who should construct bleachfields.
Several persons offered to make fields; and it was agreed that they should
receive L.50 for each acre of ground so laid out. Considerable sums were
also paid for the introduction of improved modes or appliances for dressing
flax. A dispute arose at Irvine in 1732 as to the adjudication of the
housewives' prize for making linen cloth. On reference to the Board, the
prize was given to the wife of the minister of Dreghorn. At that time the
linen manufacture was reported to be in a flourishing condition, and it went
on steadily increasing till 1740. During that year the manufacture of coarse
linens met with a serious check from the severe frost which prevailed in the
winter season. The weavers were badly provided with houses, and were unable
to work during the frosty weather. That circumstance, coupled with the high
price of provisions, led to many of the men leaving their employment and
enlisting in the army. In 1745, L.50 was awarded to John Johnston for the
invention of an ingenious method of throwing the shuttle in broad looms. In
1750 premiums for sowing flax-seed were discontinued, owing to want of
funds. An Act of Parliament was passed in 1753 giving L3000 per annum for
nine years (in addition to the L.2000 formerly granted) to the trustees, to
be applied by them for encouraging and improving the manufacture of linen in
the Highlands. No part of the said sum was to be given for any other use
than instructing and inciting the inhabitants of that part of Scotland to
raise, prepare, and spin flax and hemp, and to weave the same into coarse
linens. This was regarded as a judicious act, calculated to wean the
turbulent Highlanders from their feudatory propensities, and to impart a
spirit of industry to them. With a view to the proper administration of the
fund, the surveyor of the Board made a tour of inspection to several
districts of the Highlands, and the report he wrote on the condition and
manners of the people excited much attention, as it revealed the existence
of a state of matters little removed from barbarism. In 1755 the Trustees
reported that the cambric manufacture established in Edinburgh by foreign
weavers had not succeeded, the prohibition against importing and wearing
French cambric having increased smuggling, and thrown great quantities of
French cambric into the country duty free. The Trustees opened a Linen Hall
in Edinburgh in 1766 for the reception and sale of goods; and for nearly
five and twenty years the hall served its purpose of accommodating the
trade. In 1790 a representation was made to the Board to the effect that the
manufacturers did not then consider the hall to be any advantage, and
therefore it was closed. There were 252 lint mills in Scotland in 1772,
distributed as follows:—Aberdeen, 7; Ayr, 22; Banff, 8; Caithness, 1;
Dumfries, 1; Dumbarton, 16; Edinburgh, 2; Elgin, 3; Fife, 11; Forfar, 31;
Haddington, 1; Kincardine, 2; Kinross, 5; Lanark, 31; Linlithgow, 4; Perth,
73; Renfrew, 3; Ross, 3; Stirling, 28. It was reported in 1773 that several
new kinds of manufacture had been introduced—such as the making of gauzes
and thread at Paisley; while the spinning of silk, wool, and cotton, had
been considerably extended. In 1787 a premium of L.100 was awarded to Mr
Patrick Taylor, Edinburgh, for introducing a mode of figuring linen
floorcloth. Many improvements in machinery, &c., are noted, and frequent
mention is made of the introduction of the modes or appliances used in other
countries. In 1790 a great step in advance was made by Messrs James Ivory &
Co., who erected at Brigton, Kinnettles, Forfarshire, a mill for spinning
yarn by machinery driven by water power. The trustees resolved to reward the
enterprise of the firm by awarding to them a premium of L.300; but, in
consequence of some matter affecting the patent, they subsequently withdrew
the award. In the same year the trustees purchased the vested rights of the
foreign weavers in Little Picardy. The weavers had found it necessary, on
account of the cambric trade not succeeding, to apply themselves to other
occupa¬tions. By the close of the century the spinning schools would appear
to have accomplished the purpose for which they had been originated, as in
the year 1800 the Board refused an application from Sir John Sinclair to
have spinning schools established in Caithness, the grounds of refusal being
that spinning was then so generally known and so easily acquired as to
render schools for teaching it no longer necessary. The awards of the Board
were not always made in the strict spirit of the constitution, as in 1802
they gave ten guineas to a man in Alyth " for his ingenuity and industry in
weaving with a wooden arm and hand." The premiums offered to the linen trade
in 1807 were for the best and second best ravens-duck, shirting, diaper,
huckaback, plain linen, &c. There were eleven prizes in all, and five of the
successful competitors belonged to East Wemyss, three to Dunfermline, two to
Edinburgh, and one to Culross. It was reported in 1821 that the crop of flax
had decreased very much, owing to the low price current. In 1822 the king
approved of L.15,000 being expended on building offices for the Trustees at
the north end of the Mound, Edinburgh. The building, now called the Royal
Institution, was completed in 1828, at a cost of L.20,424. The abolition in
1823 of the law relating to the stamping of linen in Scotland curtailed the
functions of the Trustees. The manufacturers had frequently urged the
injurious effect of the operations of the Board, and were ultimately
successful, as stated, in having all legislative interferences with the
trade abolished.
A record is preserved of the
quantity and value of linen cloth stamped in each year during which the
jurisdiction of the Board of Manufactures extended to the trade. The figures
relating to every tenth year up till 1818, as well as those for the last
four years in which the stamp-laws were in force, are subjoined:—
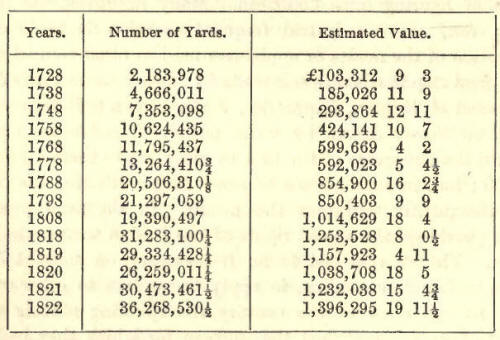
The above figures show the
development of the trade under the encouraging influences extended to it;
but the credit does not lie altogether with the Board of Manufactures. The
British Linen Company, incorporated at Edinburgh in 1746, did much good by
advancing money to the manufacturers, and helping them to dispose of their
goods. The company originated with the Duke of Argyll, and other noblemen
and gentlemen, who, finding that the linen manufacturers were frequently
placed in a position of difficulty by the fluctuations of the market for
their goods, and that sales had sometimes to be made under value in order to
raise money to meet pressing engagements, resolved to form a company for
trading in all branches of the manufacture. With a capital of L.100,000, the
subscribers of which were actuated solely by patriotic motives, the company
imported flax, linseed, and potashes, which they sold on credit to suitable
persons, afterwards buying at a fair price the yarns and linens made from
the material supplied in that way. The company had warehouses in Edinburgh
and London, in which they stored their purchases, and thence disposed of
them by exportation and otherwise. After a time, the company came to think
that they could best promote the branch of industry to which their attention
was specially devoted, by advancing money to manufacturers, and allowing
them to prosecute the trade on their own account, free from the competition
of an incorporated body. The company accordingly suspended operations as
dealers in linen, and adopted banking as their sole business. In the latter
connection the incorporation still exists, retaining its original
designation of "The British Linen Company."
For several years after the
repeal of the Act anent stamping linen, a system of inspection was in
operation; but it was entirely voluntary. The inspectors, in most cases,
were the same persons who had acted as stampers under the Act, and so were
generally well qualified for the work. Manufacturers either took their cloth
to the inspector, or, as was more commonly the case, got the inspector to go
to their factories. If the inspector was satisfied with the quality of the
cloth he stamped it with his own name. Such a system was liable to abuse,
however, and the stamps of the inspectors soon lost whatever value they had.
Merchants became better acquainted with the quality of the goods they
bought, and were content to deal according to their own judgment, without
the intervention of inspectors.
It would appear that linen
was an article available in making payments of rent in kind; for the rental
lists of the Marquis of Huntly show that in May 1600 the payments of that
description included 990 ells of linen. Dressing and spinning lint formed an
important part of the domestic duties of the wives of farmers and cottars in
those days. In an account of a tour in the Highlands of Scotland made by an
Englishman in 1618, it is stated that "the houses of the gentry are like
castles, and the master of the house's beaver is his blue bonnet; he will
wear no shirts but of the flax that grows on his own ground, or of his
wife's, daughters', or servants' spinning; his hose, stockings, and jerkins
are made of his own sheep's wool." Sixty years later another visitor
wrote:—"But that which employs great part of their land is hemp, of which
they have mighty burdens, and on which they bestow much care and pains to
dress and prepare it for making linen, the most noted and beneficial
manufacture of the kingdom." A third visitor, who came in 1725, wrote as
follows:—
"Many of the Scotch ladies
are good housewives, and many gentlemen of good estate are not ashamed to
wear the clothes of their wives and servants' spinning." Among some notes of
the manners and customs of the people of Scotland, written by a lady who was
born in 1714, is the following:—"Linens being everywhere made at home, the
spinning executed by the servants during the long winter evenings, and the
weaving by the village webster, there was a general abundance of napery and
underclothing. Every woman made her web and bleached it herself, and the
price never rose higher than 2s. a-yard, and with this cloth almost every
one was clothed. The young men, who were at this time growing more nice, got
theirs from Holland for shirts; but the old ones were satisfied with necks
and sleeves of the fine, which were put on loose above the country cloth.
Table linens were renewed every day in gentlemen's families, and table
napkins were always used. A few years after this, weavers were brought from
Holland, and manufactories for linen established in the west. Holland, being
about 6s. an ell, was worn only by men of refinement. I remember, in the
year '30 or '31, of a ball where it was agreed that the company should be
dressed in nothing but what was manufactured in the country. My sisters were
as well dressed as any, and their gowns were striped linen at 2s. 6d. per
yard. Their head-dresses and ruffles were of Paisley muslins, at 4s. 6d.,
with fourpenny edging from Hamilton—all of them the finest that could be
had. At this time hoops were constantly worn four and a half yards wide."
With reference to the linen trade, Mr Patrick Lindsay, in his book on the
"Interest of Scotland," already quoted, expresses himself strongly on the
"woeful neglect" with which it was treated at the time he wrote, in 1733;
and he makes suggestions for remedying a state of matters so undesirable.
The following extract contains some of his views:
"If all our spare and idle
hands were employed in the linen, and thereby enabled to live comfortably by
their own labour, and to bring in a little wealth to the country, the
improvement of our other manufactures might be safely left to themselves,
for it is more our interest to be served with several kinds of goods from
England, so long as they are bought cheaper in England and our linen sells
to advantage there, than to be overstocked in any branch of business which
we cannot export; and in this our greatest danger lies. Many of our young
joiners and other young tradesmen go now and then to the plantations for
want of suitable encouragement at home. Were all these supernumerary
tradesmen bred to be linen weavers, how much might this valuable manufacture
be increased, by employing in it so many more hands. As manufacture was in
no esteem, men of fortune thought it beneath them to breed their children to
any business of that sort; and, therefore, since war ceased to be our chief
trade, the professions of law, physic, the business of a foreign merchant
and shopkeeper, reckoned the only suitable employments for persons of birth
and fortune, have been greatly overstocked. Several young men, bred to no
business, pretend to turn merchants, and follow trade in the smuggling way,
and thereby do great hurt to the fair trader, and to their country, and in
the event ruin (for the most part) themselves. After the Revolution many
churches continued vacant for several years, and young men were no sooner
qualified for the ministry, than they were sure of a settlement; and even
too many were admitted (to the discredit of the profession) before they were
so well qualified for it as the dignity of the office requires. Our Church
livings are but small, and therefore few people of rank or any condition
educate their sons for clergymen; whereby these many vacancies were a great
temptation, and an encouragement to people of low rank to follow that
profession. One bad effect of this way of supplying vacant churches to the
public is, that as these clergymen have nothing but their stipends to depend
upon, unless they are frugal beyond measure, and parsimonious to a fault; if
they have wives and children, these must be left indigent, as burdens upon
the public. The case is now much altered as to vacancies, for at present we
are so overstocked with young clergymen, that one-half of the probationers
who are now candidates for the supplying of churches as they fall vacant can
never in reason hope to be provided for. The public suffers greatly under
this heavy burden of so many idle and useless hands; and of all professions,
an unemployed clergyman is the most helpless and useless member of society.
Thus it is evident that every profession, and every trade (except the linen)
is, and is very liable to be, overstocked in numbers; but the linen trade,
if duly improved, is sufficient to employ our supernumerary hands, and can
never be overstocked. The linen manufacture may be brought to as great an
extent in value as any other business now carried on in Britain, except the
woollen; and it may employ near as many hands as the woollen does. And the
linen trade of the north is of as great consequence to the nation in general
as the woollen in the south, and equally deserves the same care,
countenance, and encouragement from the public."
When the Board of Trustees
for Manufactures began operations in 1727, the manufacture of linen was
carried on in twenty-five counties of Scotland, the quantities produced in
each varying from 65 yards (valued at L.3, 7s.) in Wigtownshire, to 595,8212
yards (valued at L.13,989, 10s.) in Forfarshire. Perth, Fife, and Lanark
came next in order. Subsequently, linen was made in all the counties except
Peebles. Forfarshire kept the lead all through, and still occupies the
foremost place. In 1822—the last year in which the stamp-laws were in force,
and, consequently, the last respecting which any accurate statistics
exist—the chief seats of the trade and the quantities of linen stamped were
as follow:—Forfarshire, 22,629,5532 yards; Fifeshire, 7,923,3881 yards;
Aberdeenshire, 2,500,4031 yards; Perthshire, 1,605,321 yards;
Kincardineshire, 632,896 yards; Inverness-shire, 318,465 yards; Cromarty,
297,754 yards; Edinburgh, 129,709 yards. During the past thirty or forty
years, the manufacture of linen has died out in many towns and villages in
which it at one time formed the chief branch of industry, and has been drawn
together into the counties of Forfar, Fife, and Perth.
The following notes, drawn
chiefly from the "Statistical Account of Scotland," will show how the
manufacture was dispersed over the country seventy or eighty years ago; how
the people of some districts failed to take it up; and again how it grew and
flourished for many years in certain towns in which it is now unknown.
Beginning with the "far north," it is recorded that about the year 1790 an
attempt was made to introduce the linen manufacture into Shetland, but
without success. As the people could purchase linen cheaper than they could
make it, they did not take kindly to the new industry; and, besides, their
habits and constitutions would appear to have been ill-suited to the
vocation, for it is said that "the fair sex were so accustomed to roam about
the rocks, that they could not apply themselves with diligence to the
manufacturing business; and the constant sitting was said to have brought on
hysterical disorders." In Orkney the case was different. The making of linen
yarn from home-grown flax was introduced in 1747, and in course of time the
trade spread over nearly all the islands. The yarn made acquired a good name
in the southern markets, and from 1750 till 1785 about 250,000 spindles were
exported annually. After that time the trade gradually declined, and it was
abandoned about the close of the century. Weaving was introduced at the same
time as spinning, but it never attained much importance. The greatest
quantity stamped in any year was under 30,000 yards. The cloth was sold in
Edinburgh, Glasgow, and Newcastle, at an average price of eleven pence
a-yard. The chief cause of the decline of the trade was the low price paid
by the country agents for spinning and weaving. It is said that latterly the
most expert spinners could not earn more than twopence a-day. The
substitution of linen underclothing for home-made woollen shirts and vests
was alleged to have seriously affected the health of the people, colds and
rheumatism having become much more common among them. Before the sea fishing
received much attention from the inhabitants of Caithness, and before the
now famous pavement quarries of that county were opened up, the making of
linen cloth, and other domestic industries, were carried on by the people,
but chiefly to supply their own wants. The farmers grew small patches of
flax, which supplied the raw material, and in course of time quantities of
dressed flax were imported. At Thurso a large number of persons were
employed towards the end of last century in spinning flax for the
south-country merchants. The Custom-House books show that, in 1794 and the
two following years, 253,749 lb. of dressed flax were brought to Thurso,
which would produce 162,342 spindles of yarn. The spinners were paid at the
rate of is. and the agent 2d. a-spindle. From this it would appear that, in
the three years mentioned, the total sum paid for spinning, &c., was L.9294,
no inconsiderable amount to be set loose in those days in a poor district of
the country. In 1851 an attempt was made by Mr Peter Reid, proprietor of the
John o' Groat Journal, to revive the cultivation of flax in Caithness. Mr
Reid erected at Wick a mill for dressing flax by Schenck's process, and with
the aid of the Caithness Agricultural Society, got a number of farmers to
devote an acre or two of ground to raising flax He furnished the seed, paid
a rent for the ground, and gave prizes to those who produced the heaviest
crop per acre. At the time Mr Reid was induced to take up the trade,
agricultural affairs in Scotland were not in a prosperous state. Oats could
be purchased at 13s. per quarter, and oatmeal at 11s. per boll; and the
proposal to cultivate flax was hailed as likely to improve the prospects of
farmers. In Aberdeenshire, Fifeshire, and Lanarkshire, mills similar to Mr
Reid's were built, and inducements were offered to farmers to undertake the
cultivation of flax, and for a time it was thought that matters would turn
out advantageously for all concerned. The hopes which had been raised were
not realised, however, for in the course of a year or two the price of grain
rose, and the farmers re¬fused to have anything more to do with flax, which
they considered a troublesome crop, and not so remunerative as they had
expected. The failure of the enterprise was a sad blow to the mill-owners,
and in Caithness especially was the subject of much regret, for in that
county there is a scarcity of occupation during greater part of the year,
and the flax mill was expected to relieve in some measure the overstocked
labour market. During the few years that Mr Reid's mill was in operation,
the flax scutched at it fetched from L.50 to L.60 a-ton, a higher price than
was obtained for flax prepared at mills situated in more favourable
localities. About the close of the eighteenth century the spinning of linen
yam from flax imported from the Baltic was carried on in Sutherlandshire,
but on a very small scale. Some linen cloth was also woven for home use, and
occasionally, when the supply exceeded the demand, a few hundred yards were
stamped for sale. In Ross-shire flax and hemp were at one time cultivated.
The flax was dressed, spun, and woven to an extent which sufficed for local
requirements, and about L.500 worth of cloth was exported annually. The hemp
was converted into canvas and cordage for the fishing boats of Avoch and the
neighbourhood. Though the trade is now extinct in Cromarty, as well as in
the counties mentioned above, it would appear from the stampmaster's returns
that the inhabitants were at one time pretty extensively engaged in making
linen goods. In 1758 about 7950 yards were stamped; but during the thirty
years following there was a con-siderable falling off, followed, however, by
a somewhat sudden and extensive revival. Thus, while the number of yards
stamped in 1788 was 4656i, valued at L.186, 8s., in 1822 the figures were—
yards stamped, 297,754; value, L.13,461, 17s. At Inverness—a town which
possesses great natural facilities for carrying on manufactures, though
these have been very little taken advantage of—a large hemp factory was
established in 1765, and for some time was so prosperous as to employ 1000
hands. The hemp was brought from the Baltic, and was chiefly converted into
sacking and tarpauling cloth, a considerable portion of which was sent to
the West Indies to be used in covering bales of cotton. The factory is still
in existence, though the business done is not so extensive as it once was.
About the year 1780 an enterprising company began the manufacture of linen
thread, and for a number of years remarkable success rewarded their efforts.
They gave employment to 10,000 persons throughout the county, most of whom
worked in their own homes, their labours being superintended by district
agents, of whom there were nineteen. The earnings ranged from is. to 12s.
a-week. The flax was obtained from the Baltic ports; and when the thread was
finished, it was forwarded to London, and thence dispersed over 'the world.
The trade was taken up in some other towns, the social and commercial
circumstances of which were more favourable to its prosecution; and many
years ago, Inverness retired from competition with them. In the first year
following the passing of the Stamp Act, 10,696 yards of linen were stamped
for sale in Inverness-shire, and the quantity made increased gradually,
until in 1822 it reached 318,465 yards. From that time the trade declined
steadily, until it left the county altogether. Nairnshire also figured in
the stampers' returns, but to a limited extent, and for a brief period. In
the parishes of Elgin and Forres, in Morayshire, flax was grown at a very
early date, and in the former it appears that teind was paid on lint in the
twelfth century. About 1790 a large number of persons were engaged in
spinning flax for the southern markets, and about 50,000 yards of linen
cloth were produced annually. A like quantity of cloth was made in
Banffshire; but, in addition, nearly 5000 persons were employed in the
parish of Banff in making linen thread, in which about 3500 bales of Dutch
flax were used every year, and the value of the manufactured article was
L.30,000. The thread was sold in Nottingham and Leicester, where it was used
in making lace, &c. Competition in various quarters spoiled the trade, and
the people took to other kinds of work. In 1748 the Earl of Findlater
introduced the linen manufacture into the parish of Cullen. At that time the
Earl was President of the Board of Manufactures, and the mode in which he
carried out his object is thus recorded:—"The Earl took to Cullen two or
three young men, sons of gentlemen in Edinburgh, who had been regularly bred
to the business, and who had some patrimony of their own. To encourage them
to settle so far north, he gave them L.600 for seven years, the money to be
then repaid by yearly instalments, free of interest during the whole period
of the loan. He also built weaving shops and furnished every accommodation
at reasonable rates. From his position at the Linen Board, he obtained for
the young manufacturers premiums of looms, heckles, reels, and
spinning-wheels, with a small salary for a spinning-mistress. So good a
scheme and so great encouragement could not fail of success, and in a few
years the manufacture was established to the extent desired. All the young
people were engaged in the business, and even the old found employment in
various ways in the manufacture, which prospered for half a century." But
Cullen could not escape the influences at work in other quarters, and the
trade drooped and became extinct in the early years of this century. The
parishes of Keith and Fordyce shared in the prosperity which attended the
linen trade, but were as unable to retain it as their neighbours.
The next district to be noticed is that in which the trade has survived to
some extent the circumstances which led to its extinction in the counties
farther north. Aberdeenshire was early engaged in the manufacture of linen
yarn and cloth. About the year 1745 the Board of Manufactures sent a
spinning-mistress to Aberdeen, at the request of some persons who desired to
provide employment for the working population. Pupils were readily found
among the wives and daughters of mechanics and labourers, who soon turned
out yarn at the rate of 100,000 spindles a-year, for which they were paid in
the aggregate about L.5000. The manufacture of white and coloured linen
thread was subsequently begun, and was carried to great perfection. In 1795
the thread manufacture employed 600 men, who earned from 5s. to 12s. a-week;
2000 women, 5s. to Gs.; and 1.00 boys, .1s. 8d. to 2s. 6d. At the same time
upwards of 10,000 women were employed in other parts of the county in
spinning yarn for making the thread. Several large manufactories for
spinning flax by machinery were established on the Don, near Old Aberdeen,
about seventy years ago, and for many years the trade continued in a
flourishing condition. At Huntly the trades of dressing flax and making
linen cloth were carried on for many years, during the best of which the
value of the goods produced was about L.25,000 annually. Peterhead did
considerable business in the manufacture of thread. In 1794 there were
fifty-two twist mills in the town, at which the yarn spun by women in their
own homes was made into thread. About 1200 persons were employed in the
various departments of the manufacture. Linen yarn and cloth were made in
several other parts of Aberdeenshire The quantity of linen cloth stamped in
the county in 1758 was 103,109 yards. The quantity in any year prior to
.1790 did not rise much above these figures; but subsequently a great
advance was made, and the quantity stamped in 1822 was 2,500,403 yards.
Kincardineshire claims to be the first county in Scotland in which
flax-spinning by machinery was established. In 1787 a mill for spinning
linen yarn was erected on the Haughs of Bervie by Messrs Sim & Thom, who
obtained a license to do so from the inventors of the machinery at
Darlington. The mill is still in operation, but the original machinery has
given place to more modern contrivances. At Benholm and Auchinblae, in the
same county, the linen manufacture still survives, but on a much smaller
scale than formerly. 632,896 yards of linen were stamped in the county in
1822.
The early history of the
linen trade in the counties of Forfar, Fife, and Perth, in which that branch
of industry is now almost entirely concentrated, will be dealt with when the
present condition of the linen manufactures of the country comes to be
noticed.
The average quantity of linen
cloth made in Kinross-shire, from — 1780 till 1790, was 118,434 yards, worth
about L.4500. This does not include what was made for home consumption.
Between 300 and 400 looms were employed in the trade. The yarn was spun by
women, chiefly from flax raised in the county. In 1811 a period of
depression of trade was experienced throughout the country; and the
gentlemen of Kinross-shire, with the view of ameliorating the condition of
the working population, subscribed L.4000, and began to purchase on their
own account and risk, cotton and linen yarn,. which they gave out to weavers
to be made into cloth. The result did not come up to the expectations that
had been formed of the scheme, as the market was overstocked, and the goods
could be got rid of only at a losing price. The trade was then abandoned,
and has not been tried again. In 1756 the weavers of Kinross formed a trade
union, the members of which made themselves subject to stringent laws as to
work and recreation. In order to induce all in the trade to become members,
it was enacted that "none of the weavers already incorporated, or that may
hereafter be incorporated, shall, without the consent of the whole or
greater part of the subscribers, have any correspondence with
non-subscribing weavers in the way of borrowing or lending any of the
utensils of their craft, under pain of incurring such penalties as the
incorporated members shall inflict." Small annual payments were made by the
members, and breaches of the rules were punished by the infliction of heavy
fines. It was usual, on occasions of public rejoicings or fairs, for the
president of the society to issue an order enjoining the members to conduct
themselves with decorum and sobriety, and to go to their homes at an early
hour, under pain of dismissal from the society. The co-operative principle
was adopted by the members for maintaining the funds of their union. The
records of the society show that sums were advanced to members for the
purchase of yarn, which, when made into cloth, was sold; and whatever profit
remained after the cost of the yarn and the labour of the weaver were paid,
was returned to the treasurer of the society. The linen trade was several
times started in Clackmannanshire, but it does not appear to have attained a
sound footing at any period. About the year 1748 the Duke of Argyll
introduced the manufacture at Inverary, but it prospered only for a short
time. The people. of Buteshire also gave it a trial, but without success. In
Stirling- shire, from 30,000 to 40,000 yards of linen were made annually
about the beginning of this century, but for many years past no one in the
county has engaged in the manufacture. Dumbartonshire produced 310,827 yards
of linen cloth in 1758, but after that year the trade declined, until, in
1822, only 11,331 yards were made; and the industry is now extinct. A small
quantity of linen was produced in Linlithgow. Mid-Lothian long stood high in
the trade, which was chiefly concentrated in Edinburgh, as many as 1500
looms being employed on linens in the city. The manufacturers were famous
for making the finest damask table-linen, and linen in the Dutch manner
equal to any that came from Holland. So early as 1698 there is mention of a
bleachwork having been established at Corstorphine. The following figures
show the quantity and value of the linen cloth stamped in the county in the
years named :-1728-747 yards, valued at L.198, 17s.; 1738-18,988 yards,
L.2986, lls. 9d.; 1748-236,954 yards, L.9616, 18s. 10d.; 1758-712,719 yards,
L.36,132, 16s. 10d.; 1768-389,962 yards, L.32,191, 17s. 6d.; 1778-178,290
yards, L.22,674, 16s. 2d.; 1788-244,710 yards, L.36,338, is. 2d.;
1822-129,709 yards, L.22,287, 18s. The price of the cloth made in Edinburgh
was always high on account of the fineness of the quality. While the average
price over Scot¬land was about 10d. a-yard, the price of the Edinburgh linen
ranged from 2s. 6d. to 2s. 11d. The manufacture of linen goods has long
ceased to rank among the industries of the city. Salton, in Haddingtonshire,
is noted as having been the first place in Britain in which weaving of the
linen cloth known as "hollands" was established, and the first in which a
bleachfield of the British Linen Company was formed. In the beginning of
last century the lady of Fletcher of Salton, animated by a desire to
increase the manufactures of the country, travelled in Holland with two
expert mechanics in the habit of lackeys. Her rank procured her access, with
her supposed servants, to the manufactories; and by frequent visits, the
secrets of operations were discovered, and models of the various works were
made by the disguised artisans. The parish in that way became acquainted
with two valuable processes of manufacturing— the making of pot barley, and
the weaving of "hollands;" and for several years it supplied the whole of
Scotland with those articles. In Lanarkshire linen was manufactured on an
extensive scale at Glasgow and East and West Monkland. The trade was
established at Glasgow in 1725, and for a long period formed the staple
industry of the city. Nearly 3000 looms were in 1780 employed in linen
fabrics in the Barony parish alone. Ten years later, however, cotton had
almost entirely superseded flax, and the weavers were mostly occupied in
making muslin. At present about a dozen firms are engaged in the manufacture
of flax. In 1728 upwards of 272,000 yards of linen were stamped in
Lanarkshire; twenty years later the quantity was 1,191,982 yards; in 1768 it
was 1,994,906 yards; but in 1822 only 228,692 yards were submitted to the
stampmaster. The cotton trade had become the staple of the west, and linen
was neglected. Large quantities of linen cloth were made in Renfrewshire.
The highest figures are those for the year 1778, when 1,467,935 yards were
stamped in the county—being chiefly made in Paisley, where also a large
number of persons were engaged in making white sewing thread. The art of
making this thread was introduced into the neighbourhood from Holland in
1725, and was carried on for a long time in the family of a lady, who first
learned the secret and began the trade. The linen manufacture of Paisley
gave way before the introduction of cotton, and was long ago aban¬doned. Ayr
shared in the profits of the linen trade in its early days, but many years
since the people took to other pursuits. Kirkcudbright and Wigtown made a
small show in the returns, and Roxburgh and Berwick produced from 30,000 to
60,000 yards annually. Melrose was famous for its "land linens" from an
early date, and the weavers received many orders from London and the
Continent; but the trade began to decline about the year 1770, and never
rallied. Linen was a commodity in:which a great business was done at St
Boswell's fair, held in the parish of that name; but for a number of years
past none has been offered, as the trade has died out in the district.
Of 197 flax, hemp, and jute
factories ascertained to be in existence in Scotland in September 1867, 176
were situated in the counties of Forfar, Fife, and Perth. This concentration
of the trade has, as already shown, taken place in comparatively recent
years, and the causes of it are not difficult to discover. The human hand,
aided only by the rude appliances of ancient times, can ill compete with
modern machinery propelled by steam; and manufacturers in places where
circumstances were adverse to the introduction of the tireless agent,
naturally found it impossible to succeed in a competition with people more
advantageously situated. Hence the spinners and weavers of linen in the
outlying districts had to relinquish their wheels and looms, and follow the
trade to the absorbing centres, or seek new kinds of employment. The change
caused much hardship, and broke up many homes. Not a few of the weavers had
been able, in the more prosperous days of the trade in the rural districts,
to acquire little freeholds, on which they lived with their families in the
midst of happiness and contentment; and it was a sad day when the failing of
occupation compelled the sons and daughters to leave the parental roof and
go, it might be, many miles away to find a market for their labour. In the
long run, the change has been advantageous to a much greater number of
persons than those who suffered by it, and now its effects are almost
entirely obliterated, if not forgotten.
The linen and jute
manufactures are almost the only branches or Scotch industry dealt with in
this book which have previously had their histories written. A few years ago
Mr Alexander J. Warden, merchant, Dundee, published under the title of "The
Linen Trade, Ancient and Modern," an exhaustive and thoroughly trustworthy
treatise on every department of the manufactures referred to, and from a
second edition of the work, issued in 1868, some valuable information here
embodied has been drawn. Mr Warden gives the following statistics relating
to the flax, jute, and hemp factories of Scotland, as existing in September
1867
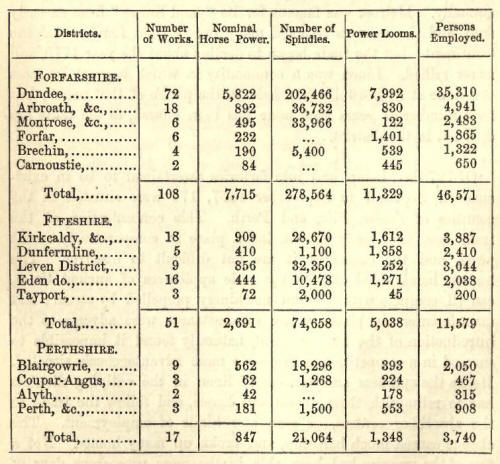
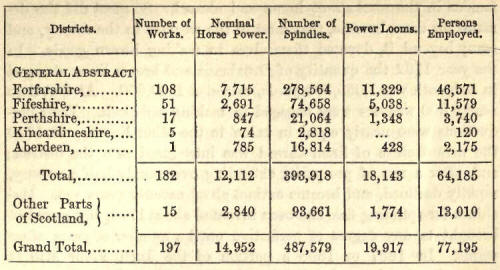
It will be seen from the
above figures that Forfarshire has considerably more than half of the entire
linen trade of Scotland. Putting Dundee aside for more special notice
afterwards, _Arbroath claims first attention. Though the conversion of flax
into cloth was practised on the banks of the Brothock for a number of years
previously, it was not until about 1738 that the trade began to assume
importance. The first impulse to the manufacture arose from one of the
Arbroath weavers accidentally discovering the mode of making the variety of
linen cloth called "Osnaburg," after the place in Germany where it was first
made and from which it was imported. The man had worked up a quantity of
flax which was unsuited for the kind of cloth then in demand in the home
market, and on taking his web to a merchant offered to give him a bargain of
it. The merchant recognised the similarity between the web the weaver was
disposed to look upon as almost unsaleable and the Osnaburg cloth; and not
only purchased the piece, but gave an order for some similar webs. The
weaver reluctantly accepted the order, little dreaming what a fortunate
discovery he had made. Before many months had elapsed, a large number of
weavers in the town and neighbourhood were engaged in the production of
Osnaburgs; and thus was laid the foundation of the almost uninterrupted
prosperity which the linen manufactures of Arbroath have enjoyed. Soon after
the discovery was made, a number of gentlemen of property in the town formed
themselves into a company for the manufacture of Osnaburgs and other brown
linens. They obtained the best machinery that was then known in the trade;
and, by devoting great care to the manufacture, succeeded in producing a
better quality of goods of the kind than was made elsewhere, and the brown
linens of Arbroath became famous in the markets at home and abroad. So great
did the demand for them become, that most of the weavers in the county, and
many beyond it, devoted themselves to making brown goods. In the year 1792
the quantity of Osnaburgs and brown linen stamped in Arbroath was 1,055,303
yards, valued at L.39,660. At that time nearly 500 weavers were engaged in
making sail-cloth. Their productions were nearly equal in value to the other
linens. In 1740 the manufacture of linen thread was introduced into the
district; and, after a run of prosperity extending over nearly half a
century, rapidly declined, and became extinct about seventy years ago.
Machines for spinning flax had been invented about 1790, but were not
brought to any degree of perfection until a number of years afterwards. In
1807 or 1808 a portion of the Inch Flour Mill at Arbroath was devoted to
giving the spinning machinery a careful trial. The efficiency of the
machines having been established, the flour grinding gear was cleared out,
and the entire mill devoted to flax-spinning. Subsequently additions were
made, and the mill is still in operation. The experiments at the Inch Mill
were watched with much interest; and when their entire success was
demonstrated, a change came over the trade, and the erection of factories
was proceeded with rapidly. A period of extraordinary prosperity set in
about 1820, and continued for five years. What followed is thus recorded by
Mr Warden:—" During this halcyon era were erected many spinning and other
works of an extent greatly beyond the means of the proprietors, and very
much beyond the legitimate requirements of the trade. There was then a
plethora of banks in the town, and in their competition for business
unwarrantable facilities were afforded to men without capital, and many of
them without experience or judgment. The natural consequence followed when,
in the beginning of the year 1826 (a year memorable in the annals of the
trade for the dire calamity which then burst upon the commercial world), the
manufactures of the place were all but unsaleable, money became scarce,
credit failed, and almost the whole manufacturing community, adventurer and
honourable merchant alike, were engulphed in one common ruin. Almost every
mill and factory was silent, distress prevailed throughout the town, and it
was some time before Arbroath became its former self again." In 1832 there
were sixteen spinning mills in Arbroath and its immediate neighbourhood; but
these were not so extensive as those at present in operation. The rates of
wages then current were:—Men from 10s. to 15s. a-week; women, 4s. 6d. to 5s.
3d.; boys and girls, 3s. 3d. to 3s. 6d. Ten years later the quantity of flax
spun annually in Arbroath was about 7000 tons, and the value of the yarn,
L.300,000. There were then employed 732 linen weavers, of whom a third were
women, and 450 canvas weavers, of whom about a fifth were women. In 1851
eighteen firms were engaged in the staple trade of the town. The horse power
of their engines was 530; the number of spindles, 30,342; power-looms, 806;
persons employed, 4620. These figures show, by comparison with the preceding
table, that during the seventeen years ending with 1867, the trade had not
increased much. It has, however, been maintained in a healthy state, and the
quantity of canvas made in Arbroath annually is about 500,000 pieces.
In the early years of last
century an annual market for linen yarn was held at Montrose, and thither
manufacturers from the adjoining counties repaired to dispose of their
goods. The making of sail-cloth was the first manufacture of any consequence
established in the town. It was begun in 1745 by a company, whose success
induced others to embark in the trade. The result was that it was overdone,
and canvas-weaving became almost extinct. Pennant states that, when he
visited the town in 1776, considerable business was being done in the
manufacture of sail-cloth, fine linen, lawns, and cambric. He adds that "
the men pride themselves in the beauty of their linen, both wearing and
household, and with great reason, as it is the effect of the skill and
industry of their spouses, who fully emulate the character of the good wife
so admirably described by the wisest man " The flax manufacturers of the
district readily adopted the machinery which had been invented for spinning,
and the first factory was built in 1805. In 1834 there were four large
factories in the town, all of which were worked by steam power. Besides
these, there were three factories on the North Esk, owned by Montrose firms,
and propelled by water. The aggregate spinning power was equal to the
production of 1,157,093 spindles of yarn annually. Some of the yarn was
woven in the town and district, but the greater part was sold to
manufacturers in other towns, or exported. The quantity of canvas and other
fabrics made in the town and neighbourhood was then about 50,000 pieces.
Though the factories have not increased in number since 1834, the productive
power of all has been extended. About 50,000 tons of flax, tow, &c., are
used annually. In addition to the persons engaged in the factories, a large
number of hand-loom weavers are employed. The chief characteristic of the
trade in Montrose is its steadiness, resulting from the caution of the
manufacturers.
When the people of Forfar
took up the linen trade, they de-voted their chief attention to weaving, and
to that they have adhered throughout, obtaining their yarns from other towns
which, like Montrose, are for the most part engaged in spinning. In 1792 the
linen weaving trade was in a flourishing state in Forfar. The principal kind
of cloth made was Osnaburg, and from 15s. to 20s. were paid for weaving a
piece of 120 yards in length, which occupied a man eight or ten days,
according to his ability and industry. In the early years of this century
the quantity of linen stamped in Forfar annually was about 1,800,000 yards;
and from 1816 till the abolition of the stamp laws in 1822, it was over
2,600,000 yards. Five and twenty years ago 3000 hand-loom weavers were
engaged in weaving coarse linens, of which about 2000 pieces were produced
weekly; and the value of the yearly produce would not be less than
L.250,000. Since that time the trade has increased considerably. The
manufacturers, having found that they could not compete successfully in the
markets unless they followed the example of other places and adopted the
power-loom, have introduced that machine; and the hand-looms, of which
nearly 5000 were in use a few years ago, are being gradually discarded.
Upwards of L.100,000 is spent annually in wages among the linen workers of
the Forfar district. The linens made are chiefly of the brown kind; and the
manufacturers have long been celebrated for the uniform and sterling quality
of their goods.
In the parish of Brechin flax
was cultivated at an early date; and after the manufacture of Osnaburgs was
established in the country, the people paid increased attention to the
cultivation of the fibre, and also to working it up into cloth. The quantity
of linen stamped at Brechin in the beginning of last century was upwards of
500,000 yards a-year, and in 1818 it reached 750,000 yards. The number of
persons employed in the trade at present is less than it was thirty years
ago; but the production is much greater, owing to the extensive introduction
of improved machinery. The premises of the East Mill Company are very
extensive. Though the original building was considered to be a large concern
in its day, its bulk is insignificant in comparison with the additions that
have from time to time been made. Up till a few years ago all the weaving in
Brechin was done by hand, but now there are three power-loom factories in
operation. There are two extensive bleach-fields in the town, capable of
bleaching about 4000 tons of yarn a-year. The principal fabrics made are
bleached shirtings, dowlas, and similar goods.
Eirriemuir, another
Forfarshire town which has retained its connection with the linen trade
through all its changes, is in the singular position of doing a large and
prosperous weaving trade by means of the hand-loom alone. In 1805, and the
two years following, the quantity of linen stamped in Kirriemuir averaged
2,226,200 yards a-year. In 1833 it was calculated that the rate of
production had increased to 6,760,000 yards annually; and at present it
cannot be less than 9,000,000 yards. About 4000 persons are employed, of
whom more than one-half are weavers. The manufacturers are disposed to erect
power-loom factories; but hitherto they have been unable to obtain suitable
sites. In the local history of the town, the name of David Sands, a weaver
of extraordinary ingenuity, who lived about the year 1760, is mentioned. He
invented a mode of weaving double cloth for the use of staymakers, and
subsequently succeeded in weaving and finishing in the loom three shirts
without seam. One of these he sent to the king, one to the Duke of Athole,
and the third to the Board of Manufactures.
In various other quarters in
Forfarshire, spinning, bleaching, and weaving linen are carried on, but
chiefly for manufacturers in the towns mentioned above.
The history of the linen
trade in Perthshire differs little from what has been recorded respecting
other counties. Blairgowrie is the chief seat of the manufacture—nine of the
seventeen firms in the county having their works on the banks of the Ericht
at that place. In the end of last century the linen trade was carried on in
no fewer than twenty-seven parishes of the county. 477,743 yards of linen
cloth were stamped in Perthshire in 1728; 793,228 yards in 1758; 2,651,674
yards in 1778; and 1,605,321 in 1822, the last year in which the stamp-laws
were in force. In the New Statistical Account of Scotland a curious remark,
emanating from this county, is made respecting the effect of spinning mills
on a rural population. The reporter from Caputh (writing so recently as 1839
be it remembered) says:—"Happily for the peace and purity of our quiet rural
population, no spinning mills have yet been erected, neither is any great
public work going on at present in this parish."
The figures relating to
Fifeshire show that, while the number of factories in that county is close
upon half the number in Forfarshire, the persons employed show a marked
difference in proportion, indicating that the factories of Forfar are, on
the average, more extensive than those of Fife. It will also be observed
that, in proportion to the spinning power, the number of power-looms at work
in Fife is greater than in Forfar—the number of spindles to each loom in the
former being about fifteen, while in the latter it is nearly twenty-five.
Kirkcaldy is the chief seat of the trade in Fife, and possesses some fine
mills. Though the art of making linen was known and practised in the
district about 200 years ago, the quantity produced was insignificant until
about 1743, when upwards of 300,000 yards were stamped in the town annually.
Kirkcaldy did not make the whole, however, as the figures include the cloth
brought in from Abbots- hall, Dysart, Leslie, &c., to be stamped. An annual
market for the sale of linen cloth was established in 1739, and various
other steps were taken by the magistrates to extend the trade.
Handkerchiefs, checks, and coarse ticks were the kinds of goods first made;
but the market for these having been spoiled by the war of 1755, which
interrupted communication with America and the West Indies, trade became so
bad that nearly all the looms were standing idle, and the manufacturers were
considering how to employ their capital more profitably. Before abandoning
the linen trade, however, Mr James Fergus resolved to try to produce
something that would sell in the home market. He studied the making of
"ticking," and succeeded in producing a fabric of first-rate quality. This
new branch of the trade was readily adopted by the desponding manufacturers,
and since then ticking has been one of the principal articles made in the
town. Towards the close of last century it was calculated that up-wards of
1,000,000 yards of linen, worth about L.50,000, were made annually in
Kirkcaldy. In 1818 the quantity stamped in the town (including the produce
of the neighbouring towns and villages) was over 2,000,000 yards. About
one-seventh of the linen made was from home-grown flax, the remainder being
made from flax imported chiefly from Riga. In 1793 three flax-spinning mills
were erected at Kinghorn, and two large spinning mills belonging to a
Kirkcaldy firm have long been in operation in that town. The number of
persons employed in the linen manufacture in Kirkcaldy about seventy years
ago was nearly 5000, and their average earnings did not exceed L.7 a-year.
The next statement of wages applies to the year 1838, when the net weekly
earnings of linen weavers averaged 7s. 3d. for ticks; 5s. 11d. for fine
sheeting; 3s. to 6s. 6d. for dowlas; and 9s. 3d. for sail-cloth. In the year
1821 a power- loom factory was built in the town, and is supposed to have
been the first establishment of the kind. The late Mr James Aytoun, of
Kirkcaldy, made some important improvements in the machinery used for
spinning flax, and adapted it to the production of yarn from tow. During the
past six or seven years the trade of the district, which had remained almost
stationary for twenty years, has been considerably extended, the additions
made to the spindles and looms being equal to nearly 100 per cent. There is
an extensive linen factory at Dysart, owned by Messrs James Normand & Son.
At Leslie several extensive
mills, beautifully situated on the banks of the Leven, give employment to a
large number of persons. These mills are owned chiefly by Messrs John Fergus
& Co. and Messrs D. Dewar, Son, & Sons, of London. Power-loom factories have
recently been erected at Tayport, Auchtermuchty, Falkland, Kings- kettle,
Ladybank, Strathmiglo, and elsewhere in Fife, all indicating that the trade
of the county is in a healthy state.
Dunfermline is the chief seat
of the manufacture of table linen. in Britain—indeed, it may be said, in the
world. When the linen trade was established throughout Scotland in the
beginning of last century, the people of Dunfermline shared in its profits,
and always aimed at the production of a high class of goods. They were most
successful in making table linen, and to that branch they have mainly
adhered. Long ago they had outstripped all competitors in their staple
industry, and the produce of their looms has for many years graced the
tables of royalty at home and abroad. At the Exhibitions of 1851 and 1862,
the goods shown by Dunfermline manufacturers attracted much attention, and
helped to extend their fame.
In the early days of the
linen manufacture only coarse goods were made in Dunfermline—first the
variety known as "huckaback," and subsequently "diapers." The weavers appear
to have been rather fond of trying the more difficult kinds of work, and
some of them adapted their looms to producing novel patterns of cloth. Great
ingenuity was also expended in weaving articles of dress without a seam. In
1702 a weaver in the town made a seamless shirt in the loom, and a like feat
was afterwards successfully accomplished by others. Two of those novel
productions are worthy of mention. In 1821 Mr David Anderson completed in
the loom a gentleman's shirt elaborately ornamented. It was of very fine
linen, and bore on the breast the British arms, worked in heraldic colours
and gold. For the accomplishment of the work he received L.10 from a fund
which had been formed in Glasgow for the encouragement of inventions and
improvements in manufacturing. The shirt was presented to His Majesty George
IV., who was graciously pleased to accept it, and to order L.50 to be sent
to the maker. Mr Anderson subsequently wove a chemise for Her Majesty Queen
Victoria. It was composed of Chinese tram silk and net-warp yarn, and had no
seams. The breast bore a portrait of Her Majesty, with the dates of her
birth, ascension, and coronation, underneath which were the British arms and
a garland of national flowers. The flag of the Weavers' Incorporation is
also a remarkable piece of work. It consists of a solid body of silk damask,
bearing a different design on each side, and yet both are interwoven.
Damask weaving was introduced
into the town in 1718, and the story of its introduction is somewhat
curious. Mr James Blake, a man of ingenuity and enterprise, went from
Dunfermline to Drumsheugh, near Edinburgh, where damask weaving was carried
on. The process of weaving was kept a close secret; but Blake was determined
not to be frustrated in his mission, which was to find out the secret and
work it for his own advantage. Feigning to be of weak intellect, he lounged
about the workshop in which the damask looms were employed, and ultimately
ventured in. The expression on his countenance when he saw the looms was so
full of puzzled wonder that the weavers allowed him to gratify his curiosity
by minutely examining the machines. He asked to be allowed to creep under
one of them that he might more closely watch its mysterious working. This
odd fancy of an idiot, as the workmen believed him to be, caused some
amusement; but no one objected to him going under the loom. While the
weavers were smiling at his bewildered stare, Blake was carefully noting in
his mind the manner in which the mechanism was arranged and how it operated.
He appeared to be fascinated by the looms, and was in no haste to go away.
When he did leave, however, he was in full possession of the secret.
Returning to Dunfermline, he at once began to construct a loom from memory,
and soon had the gratification of possessing a perfect machine. He had a
workshop in the old tower of the Abbey, and there, in company with one or
two faithful assistants, he devoted his whole time to making damask goods,
keeping well the secret which he had become possessed of in such a singular
way. It would appear that he was more successful in maintaining the secret
than the weavers of Drumsheugh, for his loom was the only one of the kind in
the town for many years. After the principle of the damask loom became
generally known, however, it was not readily adopted, the machine being
costly and difficult to work. Fifty years after Blake had set up his
machine, there were only ten or twelve damask looms in Dunfermline; and ten
years later, in 1778, the number did not exceed twenty. Three persons were
required to work the loom at first—two weavers, one at each side, to throw
the shuttle and move the "lay," and a boy to work a series of cords which
raised the warp threads necessary to produce the design. Sometimes one man
undertook to work a web two yards wide without an assistant, and in that
case he had to rush from one side of the loom to the other continuously in
order to keep the shuttle going. That was a laborious mode of working; but
it was more profitable than the other system, as, though a smaller quantity
of cloth was produced in a given time, that shortcoming was more than
compensated for by saving the wages of an assistant.
An important improvement was
made on. the damask loom by Mr John Wilson, of Dunfermline, who devised a
mechanical arrangement which dispensed with the services of the draw-boy.
The value of Mr Wilson's invention was publicly acknowledged by his being
made a burgess of the town in 1780; and a further reward was conferred on
him by the Board of Manufactures, who presented him with L.20. As damask was
then woven, it was necessary that the weavers should commit to memory the
details of the patterns; and when a loom was changed from one design to
another, the workmen had to devote four or five days to getting the new
pattern by rote. An error of memory was unfailingly registered in the cloth;
and as the value of the piece was thereby deteriorated, only persons who had
good memories, and who took great pains to learn the patterns, could pass as
efficient workmen. Subsequently an invention was made which rendered it
unnecessary to trust to memory for the proper working of the design. The new
apparatus was known as the "holey-board." In 1803 Mr David Bonnar obtained a
patent for what he called a "comb draw-loom," which had the effect of still
further simplifying the operations of the damask weaver. The trade gradually
increased under these various improvements in the weaving machinery; but it
received its greatest impulse from the introduction of the Jacquard machine
in 1825. By the year 1830 that machine had come into general use. The
advantages derived from the Jacquard machine are numerous; but the most
important are that the facility of production enables the damask
manufacturer to sell his goods at a lower price per yard on the average than
was formerly paid for weaving alone, taking into account also the reduced
price of the raw materials, and that there is no limit to the variety of
designs that may be produced. The designs of the damask made by the old
process were crude and indistinct, but by means of the Jacquard machine the
greatest distinctness of outline and delicacy of detail have been attained.
The Jacquard. machine makes every thread of warp and weft play its part in
the design; but by the " draw" system the pattern was brought out by moving
four or five threads at a time; the result is that the old damask looks as
if the design were worked in mosaic, each spot being a square equal to the
thickness of four or five threads, and in some cases even more. A change of
design was a serious matter for the weaver before the Jacquard machine was
introduced, as the mounting of a fresh pattern occupied five or six weeks,
and during that time he received no remuneration.
When the damask trade had
become fairly established in Dun-fermline, the manufacturers received orders
from noblemen, bishops, and private gentlemen, for sets of table linen
bearing their coats of arms, &c. His Majesty 'William IV. was their first
royal customer, and Queen Victoria had some linen made for her household in
1840. Since the latter date many orders have been received from royal
personages at home and abroad. Great attention has been paid to the
designing department of the trade, which has more than kept pace with the
mechanical improvements. In 1826 a drawing academy was established in the
town, with the view of teaching young men the principles of drawing, and
fitting them to fill the office of designers. The institution did not
succeed, and was given up in 1833. Some designers of eminence were trained,
however, and good resulted to the trade generally. The academy was supported
at the joint cost of the Board of Manufactures and the manufacturers of the
town, who expended L.126 on it annually. The Board also gave premiums for
excellence of design in damask goods, and one firm received L.516, 10s. in
premiums of that kind in eighteen years. Thirty years ago an export trade to
America was opened up by the manufacturers, and about L.150,000 worth of
damask goods found a market in the United States every year. The Americans
have ever since been good customers.
The largest factory in
Dunfermline, and the most extensive of the kind in Britain, is the St
Leonard's Power-Loom Factory, which belongs to Messrs Erskine Beveridge &
Co. The factory is beautifully situated on the south side of the town, and
is in every respect a model establishment. The main building is but one
storey high, and the roof consists of a series of ridges. Externally, the
place is unpretending enough, but there is an air of tidiness and
cleanliness in all its accessories which impresses one favourably. The
coarser sorts of yarn used in the factory are brought from Dundee,
Kirkcaldy, &c., and the finer sorts from Yorkshire and Ireland. Some of the
yarn is received in a brown state, some bleached, and some dyed. Many tons
are kept in stock in rooms set apart for the purpose. The yarn is given out
in hanks to the winders, who, by the use of simple but ingenious machines,
wind it on bobbins for the use of the warpers, or on pirns for the weavers.
The warpers take a certain number of bobbins and arrange them in a frame.
The threads of the bobbins are then led to the warping-machine, in which
they are arranged side by side, and wound with equal strain upon a roller.
One of the great difficulties that had to be overcome by the inventors of
the power-loom was the tendency which the rapid and somewhat violent motion
had to soften and break the warp. That difficulty was removed by " dressing"
the warp with paste, and for performing that operation a machine was
devised. After the yarn has been wound upon it, the roller is taken to the
dressing- machine. The yam is led between a pair of cylinders, one of which
revolves in a bath of paste made either of flour or of Irish moss; it then
passes over a number of cylindrical brushes, which smooth down the fibres
and remove the superfluous paste; next it is brought into contact with a
large cylinder heated by steam; and having been thus thoroughly dried, is
wound upon the beam of the loom. Before the warp is placed into the loom,
however, a preliminary operation is necessary. The threads have to be drawn
through the "heddles" and the "reed," and then the beam is placed into the
loom.
In following the warp to the
loom, it is necessary to enter a workshop, the floor of which is covered by
machinery, while overhead the eye gets lost in a maze of belts, shafts, and
other mechanism, the motion of which makes one giddy, while the noise
closely resembles the roar of a great waterfall with a metallic tinkle
superadded. In this workshop, which is nearly 700 feet long by 160 feet
wide, 900 power-looms are at work. Each large loom and each pair of small
looms is attended by a young woman The looms are prepared and kept in order
by mechanics and tenters, each of whom has charge of a certain number of
looms. The tenters take off the finished webs and put on fresh warps, and
the mechanics look after the working portions of the apparatus. The looms
employed in weaving damask are each fitted with a Jacquard machine, that
beautiful contrivance which, next to the loom itself, is perhaps the most
important invention ever made in connection with textile manufactures. The
Jacquard machine was invented in the year 1800, and was at once adopted by
the silk and muslin weavers of France, as it enabled them to introduce
unlimited variety into the figuring of their goods.
In the St Leonard's factory
the capabilities of the Jacquard machine are admirably illustrated. Each
loom seems to be producing a pattern different from all the others, and yet
the beauty and elegance of the designs are nearly equal. Some of the table-
covers made bear the arms and insignia of the persons for whom they are
intended, while others display designs of exquisite beauty, composed of
flowers, shields, &c. A somewhat coarse variety of table linen -worked in
brown and white yarn is made in large quantities for the American market;
but the chief produce of the establishment consists of the finest quality of
white table linen.
Most of the designs are made
by Mr Joseph Paton, the father of Sir Noel Paton, the celebrated Scottish
artist; and that gentleman has done more, perhaps, than any other to
maintain the fame of the local trade. His fine artistic taste and thorough
knowledge of the capabilities of the material that he has to work upon have
enabled him to produce designs which for elegance and appropriateness are
unsurpassed. It would appear that taste in the matter of table linen changes
as frequently as taste in matters of dress, and that the favourite design of
to-day may be a drug in the market next month. At one time a stately
classical style is in vogue, at another nothing but florid Italian will
sell, and with the next change perhaps the public taste may be met by a bit
of modern device. Sometimes the centre of the cloth is filled with elaborate
work, and the border treated in a simple way. Again, the centre is plain, or
dotted over with leaves, and the border is composed of a broad band of
flowers, &c.
The designs are drawn on
paper, the surface of which is divided by lines into minute squares, each
square representing a loop of the fabric. The paper bearing the design is
taken to the card-maker, who, by means of a curious little machine, punches
in a piece of card-board a series of holes corresponding with the design.
The cards are attached to the loom, and serve to guide the apparatus through
the pattern. The holes in each card relate to one throw of the shuttle, so
that a card is required for every thread of weft that goes to make up a
table-cover. As many as 50,000 cards have been used in making one piece of
damask When the design is transferred to the cards all trace of it is lost
until it reappears in the web on the loom; for the holes in the card convey
no idea whatever of the drawing.
Most of the white goods are
sent to Perth to be bleached, there being no convenience for conducting that
operation at the factory. The bleaching is followed by hot-pressing, which
gives a beautiful "finish" tothe cloth. Goods that have not to be bleached
are calendered on the premises. The "lappers" receive the goods from the
finishers, fold them up, and prepare them for the market. These operations
are carried on in the warehouse, a stately detached building in the Italian
style of architecture, and three storeys in height. The main entrance of the
warehouse opens on a spacious hall paved with ornamental tiles, and
otherwise decorated. On the ground floor are the counting-room, manager's
offices, and the packing-room, while the floors above are occupied by a
series of large halls, fitted with enclosed shelving for storing goods, and
tables for exhibiting them upon. The whole place is handsomely fitted up.
In addition to the 900
power-looms in St Leonard's factory, Messrs Beveridge & Co. employ 180
hand-looms in a separate workshop. Altogether they give employment to about
1500 persons, of whom about ninety per cent. are females. The quantity of
linen made by the firm averages about 200,000 square yards a-week, so that
the yearly produce, supposing the average width of the web to be one yard,
amounts to 10,400,000 yards, or upwards of 5900 miles, which would be
sufficient to cover a board at which the entire population of Scotland and
Ireland might dine at one time. The value of the cloth made is about
L.360,000 a-year, and the price per yard ranges from 5d. to 5s. The women
and girls employed in the factory earn from 4s. to 15s. a-week, and the men
from 10s. to 40s Many of the women and a few of the man live at a
considerable distance, and, when they go to work in the morning, take their
day's provisions with them. Two large dining-halls are provided for their
accommodation at meal time. These are comfortably fitted up, and adjoining
them is a large stove for warming food. Provision is also made for the
education of the children of the workpeople. A school-house has for many
years been in existence in connection with the factory. The school is open
to the public generally, but there is this difference—while the children of
persons connected with the factory are charged only half the established,
fees, other children have to pay full. There are usually about 300 children
in attendance.
Next in extent to St
Leonard's is the Bothwell Power-Loom Factory, built about five years ago by
Messrs D. Dewar, Son, & Sons, of London. It has accommodation for 580
power-looms, but only 470 have yet been set up. Upwards of 500 persons are
employed. The goods made are similar to those produced at St Leonard's. Two
other factories have recently been erected—one for Mr Alexander, fitted with
between 400 and 500 power-looms; and the other for Messrs Inglis & Co., with
about 300 power-looms. Messrs Andrew Reid & Co., and Messrs Henry Reid &
Son, who have long been engaged in the trade, have made considerable
additions to their factories, which now contain about 300 power-looms each.
There is another power-loom factory occupied by Messrs Hay & Robertson, but
it is of small extent compared with those mentioned. In Mr Darling's factory
there are 180 hand-looms.
It is calculated that there
are scattered throughout the town and suburbs from 600 to 700 hand-looms,
which, with those in the factories of Messrs Beveridge and Mr Darling, give
a total of, say, 1000 hand-looms at present in operation. The total number
of power- looms is 2670, and the quantity of cloth made annually by hand and
power is over 30,000,000 square yards, which, formed into a web of the
uniform width of one yard, would measure the distance between Great Britain
and New Zealand, with a thousand miles or so to spare. There is more linen
cloth manufactured in Dunfermline than was made in all Scotland in any year
preceding 1822, and the value of the goods produced cannot be much under
L.2,000,000 a-year.
Mr Balfour, the designer at
the Bothwell factory, produced a piece of work about ten years ago which
excited much attention. It was styled "the Crimean Hero Tablecloth," and
many copies of it were supplied by Messrs Dewar to royal and other orders.
The cloth was pronounced to be the greatest achievement in damask work ever
accomplished. It is thus described in Chalmers's "History of Dun¬fermline:"—
"The designing and executing
of the work occupied about eight months, and occasioned an outlay of nearly
L.600. The cloth was inspected and greatly admired by the Queen and Prince
Albert at Balmoral, as also by the Emperor and Empress of the French. at
Paris, who gave an audience to the proprietor, introduced to their majesties
by the Earl of Clarendon. Orders were given for the imperial as well as
royal tables. The cloth is composed of the finest linen warp and white silk
weft, six and a-half yards in length, and three in breadth; but when wrought
for sale, it will consist of linen only. The pattern consists of a
beautifully elaborate leafy scrollwork for border, in which, at proper
intervals, are inserted twenty- four faithful portraits. In one end-border
are Her Majesty Queen Victoria in the centre, and on either side the Prince
Consort and the Duke of Cambridge. In the other end-border are the Emperor
Napoleon in the centre, and on either side the Empress Eugenie and Prince
Napoleon. In the centre of one of the side-borders is placed the King of
Sardinia, and on either side Bosquet, Brown, F. Nightingale, La Marmora, St
Arnaud, Cardigan, Raglan, and Bruat. In the other side-border, the Sultan in
centre, with Omer Pasha, Williams, Canrobert, Evans, Campbell, Pelissier,
Lyons, and Simpson, on either side. Each portrait of the sovereigns is
surmounted with their respective armorial bearings, placed towards the
middle of the cloth; and alternately with these are trophies containing the
names of the chief battles, with their dates—Alma, 20th September 1854;
Balaclava, 25th October 1854; Inkermann, 5th November 1854; Tchernaya, 16th
August 1855; and in the centre of the cloth there are magnificent trophies
illustrative of the fall of Sebastopol, with the motto, Deus proteget
justitiam, and the date 8th September 1855—the ground around all of these
being interspersed with the stars of the orders of the different sovereigns.
In the corners of the border are the standards of the four powers rising
from behind a shield containing their insignia united—the Rose, the
Fleur-de-lis, the Crescent, and the Cross. An idea may be formed of the
extent of the design by persons acquainted with the nature of the work, when
it is mentioned that there were 50,000 cards, and seven 600-cord Jacquard
machines employed in forming the pattern on each loom. These machines
required to be kept in operation at the same instant, and the whole was put
in motion by a single movement of the foot. The web was 1600 threes in the
reed, equal to 4800 threads upon the yard, and which, again, multiplied by
three, the number of yards in the breadth, gives the total number of threads
in the breadth to be 14,400."
Dundee is the metropolis of
the linen trade, and till recently had a monopoly of the manufacture of
jute. The perfection to which the latter branch has been brought by the
enterprise and ingenuity of those engaged in it is remarkable, considering
the comparatively brief period which has elapsed since the fibre was
introduced. Capitalists in Dundee had for many years shown a disposition to
make the place a seat of manufactures; but though they tried to establish a
permanent trade in various articles, they had little success until they
turned attention to working in flax. The date at which the manufacture of
linen cloth was begun in Dundee is not known; but it is recorded that at the
time of the union of England and Scotland 1,500,000 yards of linen were made
in the town annually. Then, as now, the chief fabrics were of the coarser
kind. A writer in the "Gentleman's Magazine" in 1742, described the linens
of Dundee as being the "poorest and meanest;" but whatever truth may have
been in that remark at the time it was written, it certainly could not hold
good in recent years. In the account which Pennant gives of his tour through
Scotland in 1776, it is stated that Dundee used to be celebrated for the
manufacture of "plaiding," which was ex¬ported undressed and undyed to
Sweden and Germany for clothing the troops of those countries; but that
trade was superseded in 1747 by the manufacture of Osnaburgs, which became
the staple trade of the county of Forfar. In 1789 there were made for sale
and stamped in the parish of Dundee 3,181,990 yards of coarse linen, valued
at L.80,587. Besides a large share of the above, there were made in the town
of Dundee upwards of 700,000 yardsjof sail-cloth, valued at L.32,000, and
esteemed to be superior in quality to any made elsewhere in Britain. The
manufacture of cotton was introduced about the year 1790, and several
companies engaged in it; but the trade survived for a few years only. During
the latter half of last century a considerable trade in the manufacture of
coloured sewing thread was carried on in the town. There were seven
companies or masters engaged in it, who owned sixty-six twisting-mills, and
employed upwards of 1700 persons. 269,568 lb. of thread, valued at L.33,696,
were made annually. The writer of the report on Dundee in the Statistical
Account of Scotland (1792) says:—" The particular cause of the increase and
prosperity of Dundee is undoubtedly the bounty allowed by Parliament on
linen manufactured for exportation. By that the industry of the inhabitants
was first set in motion and encouraged; and their consequent prosperity, if
it be not an evidence in favour of bounties in general, is at least a
decisive one that in some cases they are wise and judicious, and may be
productive of the greatest benefit."
Whatever effect bounties may
have had on the trade in its early days, the present extent and prosperity
of the staple industry of Dundee is principally owing to the perseverance of
the manufacturers in adopting and improving machinery for superseding hand
labour, cheapening production, and improving the quality of the work. Up
till the beginning of the present century, all the yarn used was spun by
hand chiefly by persons residing in the country districts; and on the
market-days the housewives brought the produce of their spinning wheels into
Dundee for sale. The manufacturers went to market and bought what yarn they
required. Great difficulty was experienced in obtaining any considerable
quantity of yarn of similar size and quality, and that defect considerably
interfered with the operations of the manufacturers, and caused them to lose
much time. The first step taken to remedy that state of matters was the
appointment of agents, who travelled through the district and purchased the
yarns from the people, carefully selecting and separating the various sizes
and qualities. Those agents also got flax from the manufacturers in the
town, and employed persons to spin it. The system continued in existence
until about forty years ago, when the spinning machinery, which had been
introduced, kept the looms fully supplied with yarn.
Flax-spinning by machinery
was first tried in Dundee, in a small mill built at Chapelside, by Messrs
Fairweather & Marr, about the year 1793. The machinery was propelled by a
ten horse power steam-engine. A second mill, of about the same extent, was
built soon afterwards; but though both were kept going for some time, the
element of success was wanting, and the enterprise was abandoned for a time.
In 1798 five spinning mills, having an aggregate of sixty horse power and
2000 spindles, were erected in various parts of the town. One of these—the
Bell Mill—was considered to be a gigantic concern at the time, the building
and machinery having cost about L.17,000. The early years of this century
were disastrous to the trade, owing to the foreign markets being in a state
of stagnation, arising from political complications and war. In 1811 only
two spinning mills continued in operation, and the Bell Mill, which had come
to a stand, was offered for sale. Between that time and the year 1822 a
great change took place in the district. In 1822 seventeen flax-spinning
mills were in operation in Dundee, all of which were driven by
steam-engines, representing in the aggregate 178 horse power. About 2000
persons were employed, and the number of spindles going was 7944. In the
neighbourhood of Dundee there were thirty-two spinning mills, containing
6978 spindles. The mills in operation in Dundee and neighbourhood in 1832
were driven by engines of 800 horse power, and the yearly consumption of
flax was 15,600 tons, which produced 7,488,000 spindles of yarn. 3000
persons were employed, and the capital invested in machinery was estimated
at L.240,000. In 1846 there were thirty-six spinning mills in Dundee, with a
motive power equal to 1242 horses, while the number of spindles was 71,670.
Five years later the number of factories was forty, but some of these were
devoted to power-loom weaving.
Experiments were made with
the power-loom in Dundee so early as 1821, but the result does not appear to
have been favourable to the introduction of that machine. Messrs W. Baxter &
Son built a factory in Lower Dens, into which they proposed to introduce
ninety power-looms; but they appear to have had misgivings as to the
practicability of weaving by power, and did not carry out their intention.
In an account of Dundee written in 1833, it is stated that " power-looms
have not been employed here, or at least not to any advantage, and they are
understood to be entirely laid aside." In 1836 Messrs Baxter built a
power-loom factory at their Upper Dens Works, and that was the first
establishment of the kind in Dundee. Three other power-loom factories were
erected soon after, but for a considerable time there was no addition to the
number.
The linen trade of Dundee has
passed through a series of crises which threatened its destruction; but it
has survived them all, and is at present in a healthy state. In 1810 the
price of flax suddenly fell from L150 to L.80 a-ton, and the effect on the
manufacturers was most disastrous. Many of them were ruined; and during the
succession of violent fluctuations which occurred in. the six following
years, few of those who withstood the first convulsion were fortunate enough
to escape bankruptcy. The stepping of the machinery threw many workpeople
idle, and great distress prevailed in consequence. Had this state of matters
continued much longer, it is not improbable that the trade would have been
abandoned; but, fortunately, a brighter day dawned for the manufacturers,
and for seven or eight years preceding 1825 they enjoyed a period of
prosperity, which helped to repair their shattered fortunes, and gave them
hopes of better things to come. In the autumn of 1825, however, the trade
was completely paralysed by the commercial panic which broke out in London,
and rapidly spread over the country. The tide of prosperity suddenly turned
in Dundee, and again many firms had to suspend payment. The stagnation of
business became so serious, that the Government were induced to lend a
helping hand to the merchants of the town, to whom they granted Exchequer
bills for goods deposited. That aid was timely, and some of the most
extensive merchants availed themselves of it. In 1827 a revival of the trade
with America took place, and things began to mend. Great quantities of
bagging for packing cotton, &c., were made for the United States, and from
that article handsome profits were realised. In 1832, the last year in which
bounties were paid on goods exported, the value of the linen sent out from
Dundee amounted to close upon L.600,000, on which the manufacturers received
L.46,854 of bounty. A fire which occurred in New York in 1835 was the cause
of the next check which the trade received. A great quantity of bagging had
been consumed in the conflagration, and the manufacturers of Dundee were
hopeful that an opportunity had occurred for profitable exertion. Most of
the machinery was set to work to produce bagging, and the result was that
the supply far exceeded the demand, and the market was spoiled. Some of the
goods sent out lay in store for years, and the price ultimately obtained
entailed serious loss. Again a number of the merchants and manufacturers
became insolvent. In order to save the trade from ruin, the banks opened
warehouses, and received goods in deposit, on which they advanced money.
After a little time the trade rallied, and continued in a fair state of
prosperity until 1847, when it was seriously affected by the crisis brought
about by over- speculation in railways. The experience of the linen
manufacturers of Dundee goes to prove that the calamity of war may directly
promote the arts of peace, for they profited largely by the demand created
for their goods, first by the Crimean and subsequently by the American war.
In the former case, however, some of them did not act judiciously, for
instead of regarding the demand created by the war in the East to be a
temporary one, they would appear to have looked upon it as permanent, since
they sunk a great deal of capital in extending their factories. When peace
was declared, those who had acted thus found out their mistake, and were
unable to keep the whole of their machinery going. The American war was the
most fortunate event that ever occurred for the linen manufacturers of
Dundee. Both armies became extensive customers, and for three years the
factories were kept fully employed. Great wealth was realised, and the
stability of most of the firms was so well secured by the accumulation of
capital, that they are not now likely to sink under fluctuations of trade
which would otherwise have ruined them.
Before proceeding further,
mention must be made of the introduction of jute, which has had a most
beneficial effect on the trade of Dundee. Jute is the fibre of plants of the
cochorus order, which are common in almost every part of India. In the end
of last century the East India Company caused inquiry to be made throughout
their vast territory with the view of discovering a substitute for hemp.
Among the specimens sent to this country was a quantity of jute, but no
particular notice appears to have been taken of the material. Small parcels
were sent on several subsequent occasions, and at length some of it fell
into the hands of manufacturers at Abingdon, Oxfordshire, a town famous for
its sacking, twines, &c., by whom it was spun into yarn, and used in making
carpeting. Subsequently, about the year 1824, a bale or two of jute was sent
to Dundee, to Mr Anderson, a linen manufacturer. He got his mother, who was
an adept at the spinning wheel, to make a trial of spinning it, but she did
not succeed to her satisfaction. Mr Anderson seemed to recognise the value
of the fibre, and made numerous experiments with it, but without much
success, beyond producing a coarse yarn suited only for sacking. The new
material was regarded with suspicion by the public, and goods suspected to
contain jute were difficult to dispose of. In 1822 Mr Thomas Neish, merchant
in Dundee, got a small consignment of jute from London, and tried to get
some of the manufacturers to spin it, but none of them would make the
attempt; and, after lying aside for four or five years, the jute was sold
for the purpose of being made into door-mats. Ten years after receiving this
parcel of jute, Mr Neish got another consignment, which was again offered to
the manufacturers in vain. After being much pressed by Mr Neish, Messrs
Balfour & Meldrum reluctantly resolved to make experiments with the fibre.
Success attended their efforts, and the foundation of the jute trade in
Dundee was laid. Mr James Watt, another merchant in the town, rendered great
service in bringing jute into favourable notice. For the first year or two
after the possibility of spinning jute had been demonstrated, the
manufacturers did not spin it pure, but mixed it with flax and tow. In 1835,
however, pure jute yarn was made and regularly sold in the market. The raw
material could be bought in 1833 for L.12 a-ton; but four years afterwards,
when the value of the fibre had to some extent been recognised, the price
was L.22 to L.23. The growth of jute in the popular favour will be best
shown by the increase in the quantities imported into Dundee in successive
years since 1838; and for the sake of comparison, the quantity of flax, tow,
and hemp imported in various years since 1815 is also given—

The present annual
consumption of flax in Dundee is estimated to be about 28,000 tons; of hemp,
about 1500 tons; and of jute, about 60,000 tons—in all, 90,500 tons; so that
in half a century the quantity of raw material used has increased fully
fortyfold. It may be mentioned that all the jute is imported from Calcutta.
Formerly it was sent through London and Liverpool, but considerable
quantities are now brought direct into Dundee as well as into Greenock.
Mr Warden thus describes some
of the qualities of jute:—"It is one of the most easily dyed fabrics known,
and the colours it takes on are bright and beautiful. The common dyes are
quickly applied, but they are very fugitive, and when exposed to the sun's
rays soon become faint and dull. By the common process the colouring matter
strikes little more than the outside of the fibre, and, as it were, paints
it; and this mode of dyeing requires little material, and is done at small
cost. The fibres of jute do not subdivide so minutely as those of flax, and
they are of a hard, dry nature, and to a considerable extent impervious to
moisture. It therefore requires a more complex process to make the colouring
materials thoroughly penetrate the fibres so as to make the dye lasting.
This can, however, be accomplished, and the better class of goods made of
dyed jute undergo this process, which makes the colours both brighter and
faster. It is hardly possible to make every colour perfectly fast, although
some of them are as durable as those upon other materials. Jute is very
readily brought to a rich cream colour either in the fibre, in yarn, or in
cloth. It is, however, very difficult to bring it to a full white without
injuring the strength of the fibre. Many experiments have from time to time
been made to bleach jute, but at best they have been only partially
successful, and it may be said that a perfect white has never yet been
attained without impairing strength. Fresh sound jute of fine quality can
without danger be brought to a moderate degree of whiteness; but as the
fibre gets older, exposure to the atmosphere changes it to a browner tinge,
and it then becomes more difficult to bleach. The sightly nature of jute,
the regular even thread which by the improved machinery is formed of it, and
the smooth, tidy, and clean appearance of jute cloth, are all pleasing to
the eye, and therefore attractive. These qualities, combined with its
cheapness, have served to recommend it to consumers, and bring it into
general use. Now, instead of being used stealthily by spinners, as of old,
it is the only material spun in a large proportion of the factories, and to
a greater or less extent it is used in every establishment in the town."
The effect of the
introduction of jute on the linen trade of Dundee is shown in the following
passage from a paper read before the Social Science Association at Edinburgh
in 1863, by Mr Robert Sturrock, Secretary of the Dundee Chamber of
Commerce:—"By the introduction of jute into the linen trade great changes
have been brought about. In place of sackcloth, bagging, and other coarse
fabrics being made from hemp, hemp codilla, flax codilla, and coarse tows,
they are all now entirely made from jute, and some of these raw materials
are not now known in the trade. Though much the same quantity of flax and
tow is now imported as many years ago,
the real linen trade is in this way supplemented, the quantity for-merly
required in the coarser branches being now available for other purposes. On
the first introduction of jute, it was only used for fabrics of the coarsest
description—in fact, it was then considered that it never could be used
otherwise; but from the improvements in machinery, and from gradually
increasing experience, this has been found to be erroneous. The more common
descriptions of Osnaburgs, sheetings, and many other fabrics, are now
manufactured solely from it; or these goods, in place of being made of flax
or tow as formerly, are now composed partly of tow and partly of jute. Fine
goods are also manufactured from a combination of jute and cotton. In this
manner has the linen trade again been most largely supplemented. The jute
trade has increased so rapidly, and the goods made from the fibre are now so
highly appreciated over the whole world, that, looking to the future, one is
entitled to say that in extent it will probably only be rivalled by the
cotton manufacture. The packsheet, baggings, sack¬ings, sacks, and woolpacks
of Dundee, are used in almost every quarter of the globe. When I state that
they are by far the cheapest manufactures of this description that can be
made from any raw material, it will be no matter of surprise though this
trade still continues to advance with great strides. There is still one
fabric worthy of particular notice, which owes its existence solely to jute.
It is the manufacture of jute carpets. These have nearly the appearance of
carpets made from wool; and though they are neither so durable nor retain
their colour so well, still, when I state that the cost varies from 6d. to
ls. 4d. a-yard, it is not remarkable that they should be greatly used. Rugs,
in imitation of wool, are also manufactured from the same material. The
reporters appointed by the jury on jute goods at the International
Exhibition last year, remarked, 'It is in Scotland exclusively where goods
made from jute represent a large branch of industry. This very cheap raw
material is employed there—either pure or mixed—to make ordinary brown
cloth, but more especially sacking, packing-cloth, and carpets. The jute
yarns used for carpets are of the richest and most varied colours, and are
sometimes used with cocoa fibre. Even the Brussels or velvet carpet is
imitated with success in appearance, if not in durability.'"
The flax and jute factories
of Dundee are substantial edifices. They are fitted with every appliance
that has been devised for promoting the health and comfort of the
operatives, and facilitating their work. As a rule the proprietors are
possessed of a spirit of considerate liberality towards those who toil for
them—or, rather, with them, for the life of even a prosperous manufacturer
is anything but a sinecure. Many of the employers are men who had but a
humble start in life, and have created their own fortunes by close
application to business. Some of those who were leaders in the earlier and
more trying days of the trade have retired to spend their remaining time in
the enjoyment of fortunes accumulated during years of anxious labour,
leaving sons and successors to carry on the work which they brought to such
a successful issue. Others who have attained an age and position which would
entitle them to retire, continue to work on, as if determined to die in
harness. Indications of the prosperity prevailing among the class are
abundant in the stately mansions which they have reared for themselves in
the outskirts of the town and in quieter localities adjacent.
The most extensive factory in
Dundee is that of Messrs Baxter Brothers & Co., which is entirely devoted to
the manufacture of flax and hemp. In 1822 the late Mr William Baxter—father
of the present head of the firm, Sir David Baxter, Bart. of Kilmartin—who
owned a small mill in Glamis, entered into partnership with his eldest son
Edward, and built a flax-spinning mill, with an engine of fifteen horse
power, on the Dens Burn, in the north-east quarter of Dundee. That was the
germ of the present vast establishment. The mill proved a successful
speculation, and three years after it was set going, a similar work of
double the power was built farther up the "burn." At that time other members
of the family had been taken into the partnership, and the firm was known by
the designation, which it at present bears, of Baxter Brothers & Co. Success
continued to follow the extended firm, and from time to time the mills were
enlarged, until it became necessary to introduce an engine of ninety horse
power. In 1833 they built another mill still farther up the stream, and to
that they added, in 1836, the first power-loom factory ever erected in
Dundee, and in that department alone provided employment for upwards of 300
persons. In 1846 the firm had in operation in Lower Dens Mills one engine of
ninety horse power, driving 3028 spindles; and in the Upper Dens Mills two
engines, equal together to 105 horse power, and driving 8000 spindles. In
the power-loom department they had two engines of thirty horse power each,
and 256 looms, with accommodation for nearly double that number. They had
also a calendering shop with a ten horse power engine. The site chosen for
the works originally was ill adapted for convenient extension, being on the
banks of a natural gorge or "den," as the name of the place implies. The
difficulties of the situation have been completely overcome, and the
existence of the valley becomes apparent only when one enters the
establishment, and sees how the gorge has been dammed up to form a series of
deep ponds, which intercept and retain for the use of the boilers the whole
water of the Dens Burn. The ground at Dens be-longing to the firm extends to
twenty-one acres, of which ten are occupied by buildings, courtyards, and
ponds. The extent of the buildings may be judged from the fact, that the
superficial area of the floors is not less than twelve acres, the greater
part of which is covered by machinery of the finest description. In the
spinning department there are 22,000 spindles, with the requisite preparing-
machines; and in the weaving-rooms are 1200 power-looms. In such a large
place it is, of course, necessary to distribute the steam- power, and no
fewer than twenty-two engines are employed, the combined nominal force of
which is 750 horse power. There are thirty-two steam-boilers, which consume
nearly 300 tons of coal weekly. The largest chimney has twenty-two of these
boilers connected with it. By using properly constructed furnaces, and with
good management on the part of the firemen, scarcely any smoke is to be seen
issuing from the chimneys. No recent census of the establishment has been
taken; but the number of persons employed is stated to be from 4000 to 4500,
of whom a large percentage are women or girls. 7000 tons of flax are used
annually, a quantity far exceeding what is worked up in the same time by any
other firm in the world. A considerable quantity of hemp is also
manufactured.
The factory occupies a
commanding site; and its elegant belfry and obelisk-shaped chimneys are
conspicuous objects in the view of the town obtained from the east. A wide
public street separates the upper division of the establishment from the
lower, but there is direct connection between them by means of a tunnel.
Owing to the nature of the site, and the way in which extensions were made,
the mills have an irregular appearance, which somewhat masks their extent.
The front presented to Princes' Street by the Upper Mills is, however, an
imposing piece of masonry. It is 250 feet in length, and consists of five
lofty storeys, with attics. Over the centre of the front is a statue of
James Watt similar to that which stands in Adam Square, Edinburgh. This
building forms the largest division of the spinning department. The flax is
imported in bags, which are deposited in a range of extensive warehouses. In
order to trace it through the various stages of manufacture, the visitor
must follow the flax from the stores to the heckling shops. Heckling is an
operation whereby the fibres of the flax, as they come from the scutchers,
are subdivided longitudinally into filaments of a fineness suited to the
quality of cloth to be made. In order to produce a fibre of sufficient
fineness for cambrics and lawns, only the best quality of flax is used, and
the heckling has to be done with great care on fine heckles. Before the
invention of heckling-machines the operation was performed by hand, and the
persons employed in that occupation formed a large proportion of those
engaged in the linen manufacture. The hecklers were generally a rough lot of
men, who were continually making unreasonable demands, and "striking" when
these were not complied with. The personal annoyance and interruption to
trade caused in that way led the manufacturers to devise means which would
enable them to dispense with hand heckling. Machines were invented which
performed the work as well as, and more expeditiously than, the hecklers,
and the result was that the hand hecklers were thrown out of employment. The
heckling machines used in the Dens Works are most ingeniously constructed.
The flax is taken from the bales in small bunches, and each bunch has its
ends presented to the "ending machine," which draws the fibres into a
parallel position and removes any entanglement from the extremities. The
bunches then pass to a heckling-machine, where each is spread out and fixed
between two pieces of wood, leaving the ends free. Thus held, the flax is
placed on the machine, the chief part of which consists of a revolving apron
of stout leather studded with spikes arranged in five or six bands, the
spikes increasing in fineness from the feeding side of the machine. The wood
clamps, with their dependent flakes of flax, slide along a rail placed
above, and running transversely to the apron of the machine. When a fresh
flake is laid on all the others move one space to the left, and are brought
into contact with the various bands of heckles in succession, and finally
emerge with all the fibres nicely dressed, and bearing a gloss which makes
the flax look almost like silk. The clamps are then unscrewed, the flax
fixed by the end which has passed over the heckles, and again put into the
machine, which completes the process by bringing the fresh end of the fibres
to the same degree of fineness as the other. Both sides, as well as both
ends of each flake, are brought into contact with the heckles, a self-acting
motion in the machine turning the clamps over each set of heckles. When the
flakes of flax come from the machine the second time they are twisted in the
central part, by which means each is kept separate for convenience of
handling. The occupation of the hecklers is not a pleasant one, and, to
those not acquainted with the trade, it seems wonderful how people can live
for many days in an atmosphere so laden with dust as that of the
heckling-rooms of a flax-mill. So dense is the air that it is almost
impossible to distinguish persons at the remote end of a room thirty yards
in length; but, despite that fact, the workers do not suffer so much in
their health as would be supposed. Some of them wear respirators,
extemporised from a bunch of flax; but few of them take the trouble to use
that simple preventive. The rooms are fitted with "dust extractors"—openings
in the floor, through which a strong current of air is drawn from the
room—and by these the more deleterious particles of dust are removed.
The next process is spinning, which involves several operations— such as
spreading and drawing—the object of which is to increase the fineness of the
fibres, give them a parallel arrangement, and unite them in a continuous
line or sliver. The flax is sent through the drawing-machine again and
again, until it comes forth in a smooth even band, about an inch in width
and a quarter of an inch in thickness. As the flax in this state has no
twist to keep the fibres in place, it is caught off the machine in tall tin
cans, and is not subjected to any handling. From the cans the sliver is fed
into the roving-machine, by which it is still further drawn out, and
slightly twisted. The roving is wound upon large bobbins, which are next
placed in the spinning frames, whereby the roving is drawn out to the
required degree of fineness, and firmly twisted. Some of the flax is spun by
the wet process, which better adapts it to certain purposes. In wet
spinning, the roving, in passing over the spinning frame, is made to dip
into a receptacle filled with water heated by a steam- pipe. The hot water
softens and separates the fibres, and admits of their being drawn out into a
finer thread than if spun dry, while at the same time it causes the loose
fibres to combine better with the body of the thread. The machinery used in
these processes has been much improved in recent years, and is as great an
advance upon that employed fifty years ago as the first spinning-jenny was
upon the rock and spindle. The full bobbins from the spinning frames are
passed to the reelers, who make the yarn up into cuts, heers, hanks, and
spindles, each spindle containing 14,400 yards. In some cases the yarn is
prepared for the loom directly from the spinning frame; but generally it is
bleached first. Messrs Baxter are the principal proprietors of a large
bleachfield, and are also the chief employers of several works of the same
kind in the district. It would be impossible to conduct the bleaching at
their mills in town in consequence of the smoky atmosphere and scarcity of
water.
Leaving the bleaching process
to be described afterwards, we shall follow the yarn through the other
departments. In the winding and warping lofts the hanks of yarn are placed
on a frame and wound upon bobbins for the warping-machines, or upon pirns
for the shuttles. After the yarn is warped it is dressed by being coated
with paste; and when the threads have been drawn through the heddles and
reed, the yarn, together with the beam on which it is wound, is placed in
the loom. These processes have already been described. At the Dens Works
they are all carried on in lofty, well- ventilated, and well-lighted rooms.
The weaving department, in
which, as already stated, 1200 power- looms are employed, is broken up by
the peculiar construction of the factory; but the principal section of it
presents an interesting sight. In a noble apartment most conveniently
situated 754 looms are congregated, and a walk along the avenues between the
lines in which these are arranged affords an opportunity for seeing the
various kinds of fabrics produced by the firm. The principal is navy
sail-cloth, of which an immense quantity is made, the chief supply for the
British navy being furnished at present, as for many years past, by Messrs
Baxter & Co. Bleached and brown sheeting, ducks, paddings, towellings,
hammocking, Osnaburgs, and Hessians, are among the other goods manufactured.
The total quantity turned out yearly is about 20,000,000 yards. When the
webs are taken from the looms they are passed through rubbing-machines,
which, by a peculiar action, draw the warp threads closer to each other, and
give a more solid body to the cloth. A web, which in the loom measures
forty- two inches in width, will, after being rubbed, measure two inches
less, and its length is at the same time increased. The cloth is next picked
and cropped. The cropping-machine, which is similar to that used by woollen
manufacturers, removes loose fibres and any roughness of surface.
Calendering is the next operation, and on it the appearance of the cloth
greatly depends. There are in Dundee a number of establishments solely
deveted to calendering and press- packing linen and jute goods; but in the
Dens and other extensive factories the work is done on the premises in a
special department. The calender generally consists of five massive rollers,
from five to six feet in length, set in an upright frame. Two of the rollers
are composed of paper and the others of iron, one of the latter being hollow
to admit of its being heated by steam. The rollers may be raised or lowered
by hydraulic power, according to the degree of pressure desired. The
treatment to which the goods are subjected in the calender varies according
to the nature of the fabrics. Thus the cloth may be either beetled,
sarceneted, cylindered, chested, or mangled, as may be desired, the
different style of finish given being the effect of putting the cloth
through the rollers in particular ways, and continuing the operation for a
longer or shorter period. The goods are next measured and folded by
machinery, and the pieces pressed separately in a hydraulic press worked by
steam. When the goods are made up into bales they are again put into the
press and reduced to the smallest possible bulk, the amount of pressure put
on being upwards of 1000 tons. Previous to the adoption of this mode of
treating the goods, the bales were so light in proportion to their bulk that
the vessels laden with them had to carry a large quantity of ballast. As the
bales are made up a consecutive number is painted upon each, along with the
trade-mark of the firm, &c. For the removal of the raw material and goods to
and from the factory a dozen horses are constantly employed. In addition to
the persons directly engaged in the working of flax, Messrs Baxter & Co.
employ a large staff of mechanics, who make and repair all the machinery
required about the works. The machine shop and foundry occupy an extensive
building, fitted with the finest and most improved machines and tools for
working in iron and wood, and, taken apart from the great establishment of
which it forms a component part, would he reckoned a considerable place of
its kind.
The great care taken to
preserve the health and promote the comfort of the bodies of the workpeople
has already been mentioned; and now some notice may be taken of what is done
for the improvement of their minds. Adjoining the works is a handsome and
commodious school-house, to which all employed about the establishment have
free access. Every expense connected with the school is defrayed by the
proprietors, who take great interest in the education of their operatives,
and, by a liberal distribution of prizes, encourage them to persevere in
acquiring knowledge. There has been a school in connection with the works
for upwards of thirty-eight years, but the present building is only ten
years old. The thirty-eighth anniversary festival was held in May 1868, when
upwards of 100 prizes were distributed to the pupils. The chair was occupied
by Sir David Baxter, the much respected head of the firm, a gentleman who is
known far and wide for the liberal and substantial aid which he has given to
every good cause that commended ,itself to him. The annual report of the
teacher showed that the average attendance was 570 day scholars and 356
evening scholars, making a total of 926. For the instruction of these there
are, in addition to the master and mistress, thirty paid monitors for the
evening school and twenty-four for the day school. The branches taught are
reading, writing, and arithmetic, in addition to which the girls are
instructed in sewing, knitting, and fancy work. There is a library in
connection with the school, to which the elder pupils have access. The
workpeople generally appear to appreciate the kindness of their employers,
to whom they have never given any trouble by combinations or strikes. They
are a steady, well-conducted class; but this remark, it is but justice to
say, applies equally to the other factory operatives in the town. In order
to meet in some measure the rapidly-increasing demand. for house
accommodation by the working classes, Messrs Baxter & Co. recently built a
large number of houses in the neighbourhood of their factory.
To complete the description
given above of the various operations in manufacturing flax, some account of
the bleaching process is necessary. About a hundred and fifty years ago the
Dutch were esteemed the best bleachers in Europe. Their method was to steep
the cloth for about eight days in ley made from vegetable ashes. It was then
washed out with black soap, and placed to steep for about a week in a vessel
filled with butter milk After another washing with black soap, the cloth was
spread on the grass for two or three weeks, during which time it was
sprinkled at regular intervals with clear water. All these operations had to
be repeated several times before the cloth was brought to the required
degree of purity, so that the material was for six or seven months in the
hands of the bleachers. All the fine linen made in Scotland was at one time
sent to Holland to be bleached. The Board of Manufactures paid great
attention to this department of the linen trade, and, as already stated,
granted liberal rewards to persons who established bleach-fields. The Board
paid the following sums for experiments in bleaching:— To James Spalding,
L.180; to Dr Win. Cullen, Glasgow, L.21; and to Dr Francis Home, L.100. The
first important improvement in bleaching in this country was made by Dr
Home, who for butter milk substituted water acidulated by sulphuric acid.
This greatly facilitated operations, as it enabled the bleachers to do in
twelve hours what formerly required nearly as many days. In 1785 chlorine
was discovered and successfully applied to bleaching by Berthollet, a French
chemist. An establishment for bleaching by chlorine was erected at Aberdeen
in 1787, and was the first of the kind in this country. Chloride of lime, a
substance of more convenient appli-cation, was discovered in 1798 by Mr
Tennant of Glasgow, and is now the principal chemical stuff used in
bleaching. Mr Alexander Drimmie, in 1820, substituted soda ash for potash
ley in bleaching, thereby reducing the cost of the operation, while linen
cloth might be bleached in a few days by the use of the soda ash alone,
almost without exposure on the grass. In 1825 Mr Drimmie effected a further
and important improvement by inventing a machine for washing the cloth. The
substances which require to be got rid of by bleaching are first, the
organic colouring matter naturally pre-sent in the fibre; second, resinous
and fatty bodies, also inherent in the fibre; third, weavers' dressing and
perspiration taken up during the process of weaving; and fourth, certain
saline or earthy substances. To separate these from the cloth, it is
subjected to a series of operations such as washing, boiling in lime-water,
steeping in a solution of sulphuric acid, and so forth. The cloth is then
sent to the calender and finished. Cotton loses about one-twentieth of its
weight by bleaching, and linen about one-third. There are a number of
extensive bleach-fields in Forfarshire, Perthshire, Fifeshire, &c., some
having a direct connection with linen factories, and others being carried on
as separate undertakings.
The importance to Dundee of
the introduction of jute has already been pointed out. In the course of a
few years the Indian fibre has come so extensively into use, that the
manufacture of linen on which it was grafted has been deposed from the
position which it long occupied as the staple trade of the town. In dealing
with the trade of Dundee, however, it would be difficult to dissociate flax
and jute; for, though one or two firms confine their attention solely to the
manufacture of flax, and a few to jute alone, all the other manufacturers
work both fibres, sometimes mixing them in certain proportions, and at
others keeping them distinct. The establishment of Messrs Baxter Brothers &
Co. was chosen to illustrate the manufacture of pure flax, and now some
account will be given of an equally extensive factory in which jute alone is
used—namely, the Camperdown Linen Works at Lochee, belonging to Messrs Cox
Brothers.
The village of Lochee, which
lies within the municipal boundary of Dundee, had an early connection with
the linen trade. Towards the close of last century there were nearly 300
looms in the village, and these were chiefly employed on coarse linens, of
which 4860 pieces, valued at L.12,520, were produced annually. The cloth was
bought by several merchant weavers, who disposed of it in Dundee and Perth,
or sent it into the English market. The first of those merchant weavers was
a Mr Cox, who died in 1741, and whose family are mentioned in the
statistical account of the parish, published in 1793. It is stated that the
family were then engaged in the same line, much to the credit and advantage
of themselves, and that to their industry and example the district was
principally indebted for its flourishing condition. They bought cloth from
the weavers, as their ancestors had done, and after bleaching it at their
bleach-work near Lochee, sent it into the market. The trade they carried on
would appear to have always been in a healthy state, and a gradual extension
of the bleaching department took place, until the fields in connection with
the work measured not less than twenty- five acres. At the close of the
bleaching season in 1819, when the warehouses were filled with finished
cloth, a fire broke out and consumed the whole, entailing enormous loss on
the representative of the fourth generation of the family who then owned the
premises. Instead of rebuilding the bleach-work in a permanent way, Mr Cox
ran up a few temporary buildings to serve till the expiry of his lease.
Meantime he had turned attention to the manufacturing department of the
trade, and established a weaving factory in Lochee. Mr Cox was succeeded in
1827 by his eldest son, who in 1841 took three of his brothers into
partnership with him, and these gentlemen constitute the present firm of Cox
Brothers, whose factory is one of the most extensive and complete of the
kind in Britain. Messrs Cox were among the first who made experiments with
jute, and such was their success therein, that they gradually discarded
flax, and now their vast establishment is entirely devoted to the
manufacture of jute. They have their own buyers at Calcutta, and import the
raw material direct; while they are, perhaps, the only firm in the district
who complete within their works all the operations of spinning, bleaching,
dyeing, weaving, printing, calendering, and packing.
The Camperdown Linen Works,
the chief portion of which was built between the years 1845 and 1850, occupy
eighteen acres of level ground on the north side of the village of Lochee.
The works have been constructed on a regular and well-considered plan, so as
to admit of almost unlimited extensions without interfering with the
convenience of arrangements whereby the various processes are conducted
without waste of time or labour in shifting the material about. The design
of the buildings is characterised by much neatness; and an elegance and
airiness pervade the place which show an extraordinary advance on the
notions as to what a factory should be. It is not many years since the ideal
of a factory was a hideously plain building of many low storeys, into which
the light struggled through windows about two feet square, the dust and dirt
on which it would have been considered something like sacrilege to have
removed. Anything approaching to ventilation was not thought of, and,
consequently, no provision was made for the admission of air to the sickly
operatives. Now, and particularly in the case of the factory under notice,
the storeys are from fourteen to seventeen feet in height, and every room is
thoroughly ventilated; indeed, no class of workers are better cared for in
the matters of light and ventilation than those in the more extensive
factories in the linen manufacturing districts. It may be that the Factory
Acts are to some extent to be credited with this; but it is due to the
owners of many of the factories to say that in the matters referred to they
have far exceeded the requirements of the law.
A branch line of railway
connects the Camperdown Works with the main system, and by it some of the
raw material is brought in and the finished goods are sent out. The jute is
deposited in two large stores, detached from the main body of the factory,
whence it is withdrawn as required. The first operation in manufacturing the
fibre is "batching." One of the great obstacles which the early workers in
jute had to contend with was the hard and dry nature of the fibre. They
could neither get it to spin nor weave satisfactorily. Old machines were
altered and new ones devised with the view of overcoming this peculiarity of
the jute; but none of these were successful until the idea occurred to some
one that the jute might be softened by being moistened with oil. This was
tried and found successful to a degree beyond expectation. The oil is
applied in a special apartment called the "batching-room," in which the jute
is spread in layers, each layer receiving an abundant sprinkling of oil and
water. In that condition the material is allowed to lie a certain time,
according to the season and temperature. The fibres of jute are from five to
eight feet in length, and sometimes even more, and in order to bring them to
a spinning condition, they used to be cut; but as a square end was not
favourable to complete hackling nor correct spinning, the fibres are now
torn asunder by being fastened by the ends to iron bars placed on either
side of a wheel having a number of stout spikes on its rim. After a handful
of jute is fastened to the bars, the latter are thrown forward, the spikes
strike the jute in the centre, the fibres are dissevered, and a fine pointed
end appears on each side. From this stage the processes which the jute goes
through in being converted into cloth are so similar to those to which flax
is subjected that it is unnecessary to describe them in detail. The
machinery used in the Camperdown Works is of the latest and most improved
construction, and is all made on the premises.
In the weaving-shed 700
power-looms are employed in making plain and twilled sackings, and all the
other fabrics usually made of jute; and in another part of the establishment
300 hand-looms are engaged on carpeting. The firm have paid much attention
to the last-named branch, and have brought the manufacture of jute carpets
to great perfection. For certain kinds of carpeting Messrs Cox hold a
patent, and some of their productions are characterised by considerable
beauty of design. There is an extensive dyeing shop at the works in which
all the yarns required for coloured goods are dyed. The colours used are of
the most brilliant hues, and the jute takes them on more readily than any
other fibre known. Jute carpeting is so cheap that it is within the reach of
the humblest householder. Some of it is sold so low as 8d. a-yard, and,
considering its appearance and durability, is a wonderful bargain.
A few statistics relating to
the factory will show its extent and importance in a more forcible way than
any minute description of the departments. As already stated, the works
occupy 18 acres of ground, a considerable portion of which is covered by
buildings. The area of the floors is 50,000 square yards, or about 10i
acres. The machinery is propelled by steam-engines, varying from 3 to 120
horse power; the aggregate nominal horse power is 580; and the indicated
horse power 1850. The steam for the engines is generated in 22 boilers
ranged side by side in one line. The smoke from the furnaces is carried off
by an ornamental chimney 300 feet in height and 35 feet in diameter at the
base. The chimney alone cost over L.3000. The quantity of coal consumed is
about 15,000 tons annually. There are 4300 persons employed within the
works, and, in addition to these, the firm employ 400 sack-sewers, who work
in their own houses. The wages paid are the same as those current in the
trade. 14,000,000 yards of sacking are turned out annually, and about half
that quantity of other fabrics. There is a free school for the workers, at
which there is a regular attendance of about 400 pupils. The factory
operatives are informed of the flight of time by a splendid turret clock,
which chimes the quarters.
In order to complete this
record of the linen and jute trade, it is essential that some mention should
be made of a factory devoted to the production of mixed fabrics. Messrs
James Smieton & Son, Dundee, have for many years taken the lead in
introducing new fabrics made of combinations of various materials. In 1857
they selected a piece of ground to the west of the village of Carnoustie,
and thereon built a power-loom factory, which bears the name of Panmure
Works, and is regarded by the trade as a model establishment. It is small in
size compared with the great factories which have been previously described,
but in convenient arrangement of departments and completeness of
organisation it is unsurpassed. The ground occupied by and pertaining to the
factory is about 10 acres in extent, and has a frontage to the Caledonian
Railway of 700 feet. The central part of that frontage is occupied by a fine
two-storey building, 325 feet in length. There is a siding on the railway
for the service of the factory. The waggons containing the yarn are passed
on to this siding, and brought into the works one by one. The yarns used are
respectively composed of flax, tow, hemp, cotton, and jute. Some of these
are made in Forfarshire and Glasgow, and some are imported from France and
Ireland. The weaving shed occupies a central position in the works, being
bounded in front by the main building, in rear by the calendering and
finishing department; on one side by the warping and dressing room, and on
the other by the engines and packing warehouse. The weaving shed is 180 feet
in length by 150 in width, and contains 400 power-looms. The departments in
which the successive operations are carried on adjoin each other; and the
yarn, which passes in at one side of the main entrance, makes a circuit of
the place, and emerges at the other side packed up ready for transportation.
This is an admirable arrangement, which at once facilitates operations and
saves expense. The variety of fabrics that may be produced by using
different qualities and combinations of yarn is immense. Usually there are
no fewer than 80 different kinds of cloth in the looms at one time, and the
list of fabrics made embraces upwards of 500 varieties. Mixtures of tow with
jute and of flax with jute are the principal; but a great variety of fabrics
are produced by mixing cotton with jute and cotton with flax. The quantity
of cloth made is about 5,000,000 yards annually, a large proportion of which
consists of "drills," "paddings," and "Russian sheetings " for the United
States, West Indian, and Mexican markets. Checks and stripes in endless
variety are also made for the same countries. The machinery, which is of the
most improved kind, includes 4 cropping-machines, 3 calendars, and 1 mangle,
the latter working under a pressure of 60 tons. The combined force of the 3
steam-engines in use is upwards of 200 horse power. The number of persons
employed is about 600.
About five years ago Messrs
Smieton spent L.2000 in the erection of an institute for the use of the
workpeople. The building, which is two storeys in height, is one of the
finest in or near Carnoustie, and is a handsome monument of the liberality
of the founders. The ground-floor of the institute is occupied by a house
for the keeper, a class-room, library, reading-room, and cloak-room. The
reading room is liberally supplied with newspapers and magazines, and
furnished with a bagatelle board, draught boards, &c. The upper portion of
the building consists of a fine hall, provided with a pia& and a harmonium.
The day scholars are taught in the class-room, and in the evening such of
the female workers as choose attend in the hall to receive instruction in
reading, writing, and needlework. Two teachers, and all the books,
stationery, newspapers, magazines, &c., are provided free of charge. Indeed,
the whole expenses of the institute are defrayed by Messrs Smieton, to whom
the yearly cost is about L.300. Finding that their workpeople had difficulty
in obtaining suitable accommodation in Carnoustie, the firm recently built
eighty houses in the neighbourhood of the factory.
At the close of 1867 there
were in Scotland sixteen firms engaged in the manufacture of flax, hemp, and
jute, who employed 1000 persons or upwards, the aggregate number of
operatives being 31,162, or an average of about 1948. Four of those firms
were spinners, but not weavers, and all the others were spinners and
weavers. The number of spindles employed by them was 205,454; of
power-looms, 5177; and the nominal horse power of their engines was 6057.
The works of eight of the firms are in Dundee, two in Glasgow, two in
Greenock, and one each in Aberdeen, Johnstone, Markinch, and Arbroath.
Of the great firms in Dundee,
two have already been noticed. The third in order is that of Messrs A. & D.
Edward & Co., established in 1828. Their factory is situated in the
Scouringburn, and the main portion of it consists of a fine building 300
feet in length, and five storeys in height, in which the spinning operations
are carried on. The weaving department occupies an extensive range of
buildings behind the main block. In the spinning mill there are 18,476
spindles; and in the weaving factory, 600 power-looms. All the goods are
finished and packed on the premises. The works, like nearly all those
recently built, are fire-proof throughout. The goods manufactured embrace
all varieties of flax and jute fabrics; and the establishment is
exceptional, as being the only one in the district in which linen damasks
are made on an extensive scale. The number of persons employed is 3300.
Messrs Gilroy Brothers employ upwards of 2000 persons in their Tay Works in
the Lochee Road. The establishment has a frontage of 1000 feet, of which 400
feet are occupied by a splendid block of building recently erected. The
latter is by far the largest and most imposing structure in Dun¬dee. It is
five storeys in height in the centre, and four in the wings.
The central part terminates in a pediment, in the tympanum of which the
Dundee arms are boldly sculptured in stone, and on the apex there is a
colossal figure of Minerva with her spindle and dis¬taff. The firm have
greatly extended their works since 1851. Then they employed engines of 80
horse power; now more than four times that power is required to move their
machinery. The material manufactured consists chiefly of jute. Messrs Gilroy
are extensive shipowners, and the jute used in the factory is brought from
India in their own vessels. A spinning mill, built by Messrs J. & A. D.
Grimond at Bow Bridge, Dundee, in 1857, was, and is still considered to be,
the finest structure of the kind in existence. The machinery is of the best
construction, and the building throughout is elegantly fitted up. There are
3600 spindles in the mill, and 136 power-looms in the weaving department.
Messrs Grimond have hand-loom and power-loom factories at Maxwelltown, and
altogether employ about 2000 persons. Among the goods manufactured are
carpeting, matting, and hearth-rugs. Mr 0. G. Miller owns five mills in
Dundee. They stand contiguous to each other, and all are devoted to
spinning. There are ten steam-engines of 260 horse power, 16,970 spindles,
and nearly 2000 workpeople. The St Roque Spinning Mill, and the Wallace
Power-Loom Factory, owned by Messrs W. R. Morrison & Co., are extensive
concerns. They contain 5000 spindles, 510 power-looms, and the motive power
is supplied by engines of 220 horse power. The workpeople number about 2100.
The Seafield Works, belonging to Messrs Thomson, Shepherd, & Briggs, were
started about fourteen years ago, and have had a rapid growth. They now
contain 6000 spindles, 120 power- looms, and give employment to upwards of
1000 persons. The firms out of Dundee who, at the period to which these
remarks refer, employed 1000 persons and upwards were:—Messrs Richards &
Co., Aberdeen; City of Glasgow Flax-Spinning Company; Glasgow Jute Company;
Messrs Finlayson, Bousefield, & Co., Johnstone; Gourock Rope-Work Company,
Greenock; Messrs John Fergus & Co., Prinlaws; Mr Andrew Lowson, Arbroath;
and the Greenock Sacking Company.
The following figures
compiled towards the close of 1867 represent pretty exactly the extent of
the linen and jute trades of Dundee:—The estimated quantity of yarn spun
annually in the town is 31,000,000 spindles, valued at L.3,487,500; in the
surrounding district, 29,000,000 spindles, valued at L.3,262,500—making a
total of 60,000,000 spindles, valued at L.6,750,000. Taking the power- looms
at 8000, and the quantity of cloth produced by each at 200 yards a-week, the
cloth turned out in a year will amount to the prodigious quantity of
83,200,000 yards, or 47,272 miles. The value of the yarn and linen together
is estimated at L.8,000,000. The capital invested in the factories in Dundee
is stated to be L.2,500,000 in the district of which that town is the
centre, L.2,200,000; in other parts of Scotland, L.1,000,000—total,
L.5,700,000, to which has to be added the value of the bleach-works,
calenders, &c., in the trade, which cannot be put down at less than
L.1,300,000. It takes about six months from the purchase of the raw material
before the goods can be manufactured and the proceeds drawn, so that the
stock-in-trade of manufacturers and merchants will amount to L.5,000,000. It
would thus appear that a capital of L.12,000,000 is required for carrying on
the linen trade of Scotland. |